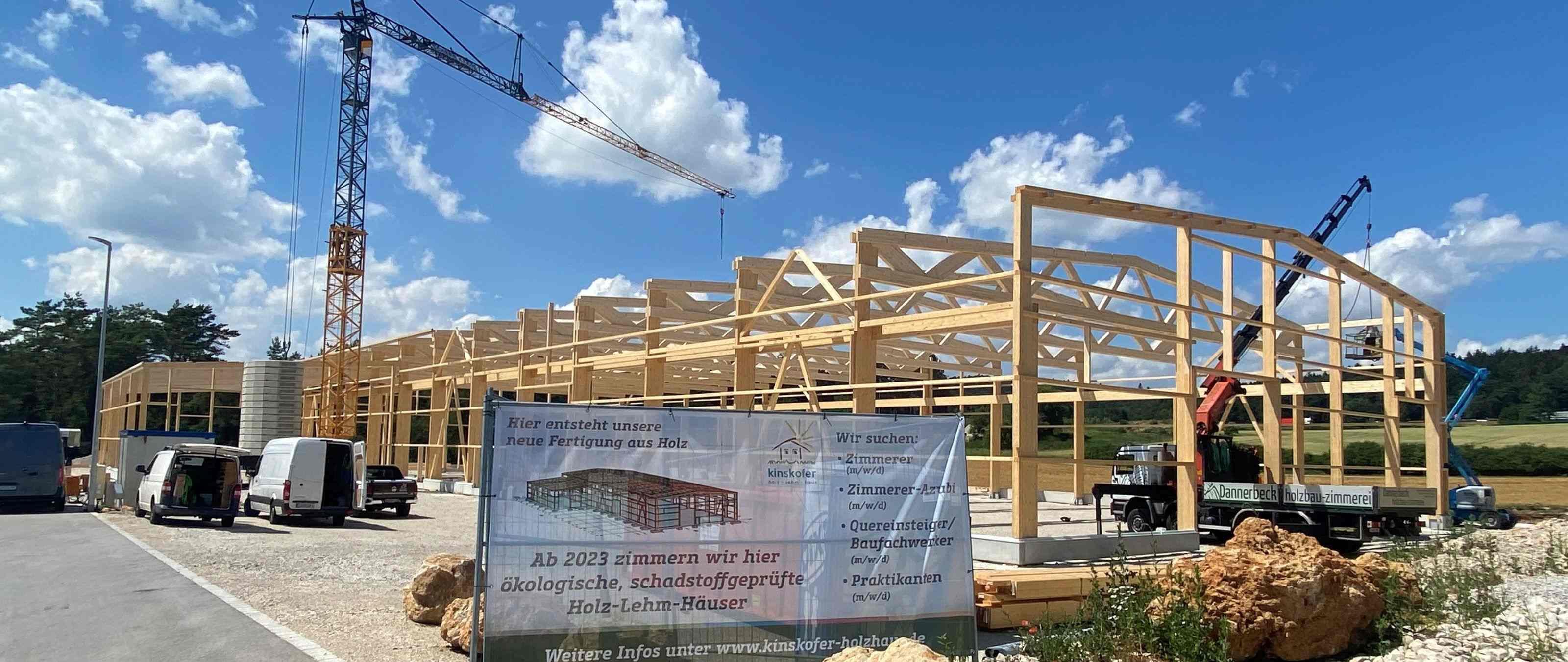
The dream of a home of one's own - the timber construction professionals of the Upper Palatinate family business Kinskofer Holzhaus know this particularly well. For over 35 years, the company has been manufacturing energy-efficient and low-emission wood-loam houses. Almost 1,000 construction families already live in a Kinskofer house. Now the Kinskofer family is preparing to realize their own dream: The successful handover to the next generation. And the new generation is gripping on tight: A new Production 4.0 with increased prefabrication level accompanies the transition and paves the way to the future. In the greenfield planning of their automated "Smart Factory" they are relying on the support of Schuler Consulting. The project team reports what the future factory and the generation change will look like.
Managing director Herbert Kinskofer has been active in ecological timber construction for over 35 years. Since the beginning of his professional career, the trained master carpenter and roofer has been committed to using the most natural, pollutant-tested materials possible on the construction site and in production. "Labels alone are not enough for us," Herbert Kinskofer emphasizes. That's why the family-owned company commissions its own measurements at independent laboratories to ensure the quality of its materials.
The company currently manufactures around 30 individual single-family homes each year. Sustainable, resource-conserving and healthy building and living has a long tradition at Kinskofer: under the impressions of conventional timber construction, the current boss decided to pursue a "green" way of building already during his apprenticeship at a prefabricated house builder in the 1970s. At that time, many pollutant-laden materials were used on construction sites. "I wanted to do better. And that meant more sustainable," the contractor recounts. The large quantities of hazardous waste generated on construction sites can be reduced to a large extent by using natural materials and reintroduced into the ecosystem. Thus was born Herbert Kinskofer's passion for ecological building and a mission for Kinskofer Holzhaus.
Sabine Kinskofer, daughter of the owner, and her partner Patrick Schramm, master carpenter, share this passion and will follow in Herbert Kinskofer's footsteps as the new management duo. In the future, true to their motto "build green - live colorfully", they want to make sustainable living possible for even more construction families. The building biologist and business economist grew up with the family business, now works as the commercial manager and continues to grow into the company management together with Patrick Schramm, who will take over the technical management as a master carpenter.
Environmental awareness plays an important role at the Kinskofers. "Since the 1990s, we have been manufacturing efficiency houses," explains the junior manager, "these houses consume less energy than prescribed. In 35 years, we have thus already permanently removed over 50,000 tons of CO2 from the atmosphere. With our new production facility, we can achieve much more!" It is not only the positive ecological effects that excite the new generation about hall construction. "With the new hall, we are setting standards for the quality of our wood-loam houses for decades to come," emphasizes Patrick Schramm.
The breathing wall
At the heart of the company's philosophy is a healthy living indoor climate. "Wood and clay as natural materials contribute to this," Sabine Kinskofer continues. The core of the wood-loam houses is the "fully diffusion-open wall," she says. Herbert Kinskofer has constantly optimized this wall structure over the years and innovatively developed it further by using new materials. Also called the "breathing wall," Kinskofer completely dispenses with foils in this wall construction in favor of diffusivity. This creates a natural indoor climate and eliminates the need for plastic. The materials used are all of natural origin. Wood fibers, jute and everything without artificial additives, such as glue or polyester.
"High quality and sustainability is the credo for the company when it comes to their wood-clay houses," reports project engineer Alexander Runge of Schuler Consulting. "When planning a new production facility, it was therefore particularly important to maintain the high quality standards and to bring greater flexibility to production through automation solutions."
The company manufactures complex constructions such as ceilings, roof trusses and fabrications for interior fittings together with a carpentry firm that supplies the wall structure and element assembly. In doing so, the timber builders rely on the proven method of timber frame construction. "A decisive advantage in this construction method is that the shell is erected in the shortest possible time, so that assembly on the construction site takes only a few days. This offers great added value for our employees, who have to spend less time on the construction site and are exposed to the weather conditions there," explains Sabine Kinskofer.
Greenfield project for the generation change
The new production facility for Kinskofer's high-quality wood-loam houses is being built on an area of around 3,000 square meters, including the warehouse. In the new production facility, further work steps such as material transport and handling, joinery and the application of planking and insulation can be automated. This speeds up the manufacturing process by over 30% percent with fewer employees. From 2023, around 35 high-quality houses with a living area of up to 250m2 are to be built here each year. "In the new hall, we are significantly increasing the degree of prefabrication. That excites me! We can now prefabricate ceilings and roof elements and even install the windows in production already. This means we are even faster on the construction site," reports master carpenter Patrick Schramm.
The fact that the woodworkers are now investing in a state-of-the-art production facility is not only due to the upcoming handover of the business. The rapidly growing market and the high demand for ecological houses are just as much the reason for the Kinskofer family to proactively set the course for the coming years now. "For us, now is the right time to invest in the future because the demands on us will continue to rise. Timber construction is currently experiencing a gigantic upswing. We will be prepared for this," says Managing Director Herbert Kinskofer, who will continue to work in the company for the long term after the handover of the business.
"We want and need to grow," confirms his successor, "but this is only possible with a sustainable manufacturing strategy that does not allow any compromises in the quality of our houses. This modern production enables us to achieve our economic goals and also remain an attractive employer for our employees, as we can, for example, make the workplaces in production even better and more ergonomic."
In the Greenfield project, the Schuler Consulting project team had the opportunity to support the Kinskofers from the very beginning. Digital solutions played a central role here, because a higher degree of automation enables the houses to be manufactured more cost-efficiently, as construction and processing times are reduced. This makes the company more flexible to respond to rising material costs and high demand.
"In greenfield project planning, we start with a site analysis and look at the site's development plan," explains project manager Volker Jahnel. "From the infrastructure in the office to the material flow in production, we have created a concept for a smart factory. Every step from POS to production, every data interface to all machines runs digitally."
"After we analyzed the capacities and process times of the new production, it was a matter of developing the individual process steps from order entry to assembly," adds project engineer Alexander Runge. "To do this, we created a technology concept that includes a machine design with several block layout variants." The development plan shows the infrastructure in and around the building with the main material flow, expansion options, all technical storage, office, warehouses, parking, entrances and exits, logistics for loading and unloading, etc. After deciding on a block layout variant, a detailed layout was worked out in scale.
Ready for the future
"In our new production facility, we will be producing with machines from Weinmann and Hundegger from 2023. The planning of our new production heralds another step towards sustainability and maximum quality at Kinskofer Holzhaus. We are glad that we have brought the experts from Schuler on board as strategic support for this," says Sabine Kinskofer.
With the new production facility, the family-owned Kinskofer company is well equipped for the future in the highly competitive growth market of timber construction, summarizes Volker Jahnel. "From our point of view, the time has come for medium-sized companies to invest in digitalization and automation now. The industry is industrializing. Those who want to be competitive are preparing now. We won't run out of demand for a long time - and neither will the material. Kinskofer has recognized this and can now grow even better."
About the project team
Herbert Kinskofer, Sabine Kinskofer and Patrick Schramm
Master carpenter & roofer Herbert Kinskofer is not only the founder, but also the creative mind behind Kinskofer Wood-Loam Houses. He has been pursuing his sustainable approach for more than 35 years, making him one of the pioneers in eco-wood construction. Together with the next generation, he is building a modern production & storage hall in 2022. Daughter Sabine Kinskofer takes over here as Betriebswirtin & Baubiologin the commercial tasks. Master carpenter and life partner Patrick Schramm will take over the technical management of the enterprise.
Volker Jahnel has been working for SCHULER Consulting in Europe for more than 30 years. Through his many years of experience as a consultant in the European and international wood and furniture industry, he specializes in the areas of process and organizational optimization, Industry 4.0 and information flow consulting, among others. Mr. Jahnel has been Senior Manager responsible for the Southern European market since 2018.
Alexander Runge has been working at Schuler Consulting for over 25 years. Worldwide, he supports timber construction companies as well as companies from the furniture industry in strategic production development. Mr. Runge specializes in planning productions efficiently, optimizing manufacturing processes and networking them digitally.