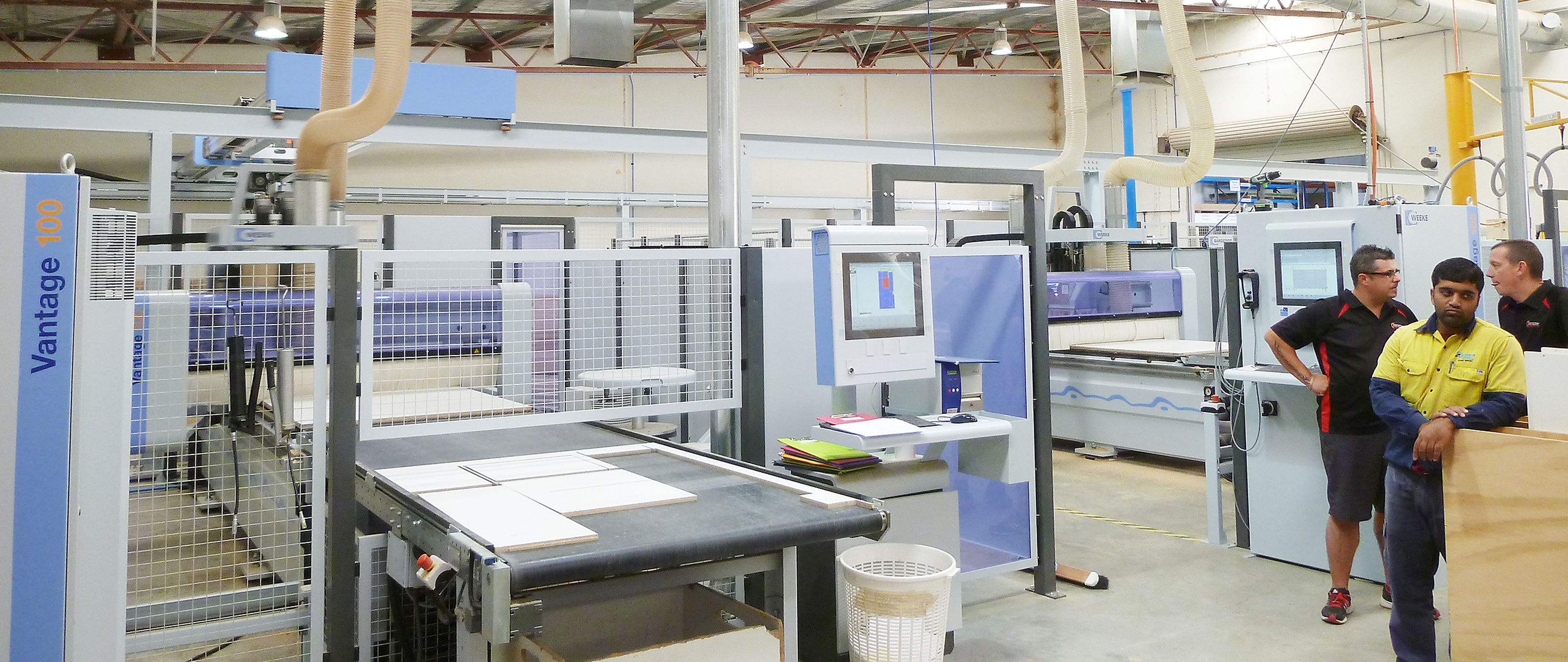
The article was first published in the AWISA Magazine, Summer edition 2015.
www.awisa.com
Short throughput times, stock reduction and flexibility with low production costs at the same time are decisive success factors for today’s cabinet making shops. Local manufacturers are constantly facing the pressure of customised products at highest quality and punctual delivery.
In order to cope with the requirements a combination of integrated, intelligent production plants and flexible, highly efficient stand-alone machining centres are necessary to remain competitive.
Perth-based company Character Cabinets have recognised the benefits of the right machinery equipment and have invested in solutions from HOMAG Australia. With a horizontal storage system, a HOMAG Automation TLF 411, and two large WEEKE Vantage 100 CNC processing centers the Western Australian company have stepped up massively in their production capacity. “The storage has increased our productivity as we could move our staff to other areas,” says business owner Squeak van Duyn.
Steady growth requires investments at the right time
Character Cabinets is proudly owned and operated in Western Australia. It is a flexible, locally-owned business that delivers kitchen design, renovations and custom cabinets of superior quality to their clients.
When a company is growing in size and staff, economic growth will not happen by itself. Innovative products and solutions do not create themselves, but are the result of the work of people who understand what is needed.
At Character Cabinets, Dutch founder and owner Squeak van Duyn and manager Nat Rowe make the final decisions. Nat, originally from Melbourne, had moved to Perth and started his apprenticeship at the age of 15 at Character Cabinets. Both know the company like the back of their hands and made it growing from a two-man team to 80 staff over a period of 18 years.
Nat says, “In the past we were cautious about investing in machines. When wages increased we had to change our approach.” Squeak had spent a lot of time in Europe to see what was happening over there in regards to machine developments. With his forward-thinking approach he could further develop the business.
At the end, they decided to partner with HOMAG. “It’s better to get a HOMAG than a lesser known brand,” says Nat. Regarding the installation process, Nat continues, “It had been a smooth transition with only a little bit downtime. We had great HOMAG techs working around us so that we could continue produce, while the new system was being set up.”
Founded 1993, Character Cabinets occupies approximately 2,100 square metres workshop space and had moved four times before they established the business in Armadale at the south-eastern edge of Perth’s metropolitan area. The enterprise enhances a reputation as a company which can be relied on as consistently delivering quality products, on time and representing real value for money.
A new era – intelligent storage systems
The base of a successful furniture production with all its procedures from the delivery of the raw material up to the delivery of the finished furniture to the customer is based on intelligent logistics. A lot of leeway in combination with operating machines and in the panel variety makes the HOMAG Automation TLF 411 to the ideal solution for highly efficient logistics for industrial production.
On span width up to 16 metres and travel way length up to 50 metres and more are almost no limits in the variation possibilities. The operation speed of up to 130 metres per minute of the storage are enormous and enable the transport of each panel to any place in the storage or the deposition of the panel in a connected operating machine. CNC operating machines are connected like saws to the storage via standard interfaces in a simplest way and turn to even more effective operating centres. “Thanks to the cell the whole workshop is cleaner and we produce less waste,” says Nat. The connection of a TLF 411 to a CNC processing combines intelligent logistics with the diversity of a CNC machine.
Nat names a few main benefits of the storage system, “It’s a sensational program, and how the TLF puts the boards away. It shows you what you need to do next without relying on the operator. We can now handle more workload. It not only shows us what we’ve got in stock but also precisely where it is. In order to avoid board sitting there, the storage uses the board. This is where the real money is!”
The TLF helps to reduce utilised capital from storing up to sawing or nesting and the material used is coordinated with the ordering system and the order planning. The TLF sets the program a night before, picks orders over night and is ready for production the next morning. Also, offcuts are managed automatically.
Driven by the industry
In addition to the storage, Character Cabinets have invested in two WEEKE Vantage 100 CNC nesting machines. “The industry has taken us to the decision of putting CNC machines in the workshop. We were busy and we didn’t have enough trained tradesmen. So we were pretty much forced into it,” says Nat.
The main reason for the investment in the new WEEKE machines was to improve the material handling. Character Cabinets’ WEEKE nesters run 13 hours a day, also in nightshifts. “We need less labour and the machines are much quicker,” Nat says. All this goes back to the service they are able to provide to their clients. Over the years, they have built up a reputation that is built on the fact that they recognise a kitchen as the centre piece of a home so each project is managed individually.
Character Cabinets supply to the building industry and retail sector but want to keep the balance between building and renovation. Squeak still looks after his private clients. They have been dealing with him for many years and still want the personal touch. Squeak describes the strengths of his company, “We deliver on time, at a price competitive rate, good quality and service.”
By having invested in the right machinery, Squeak and Nat are moving in the right direction thanks to savvy business skill and HOMAG Automation solutions and CNC machining centres.
“It’s a sensational program how the TLF puts the boards away.”Nat Rowe, Manager, Character Cabinets