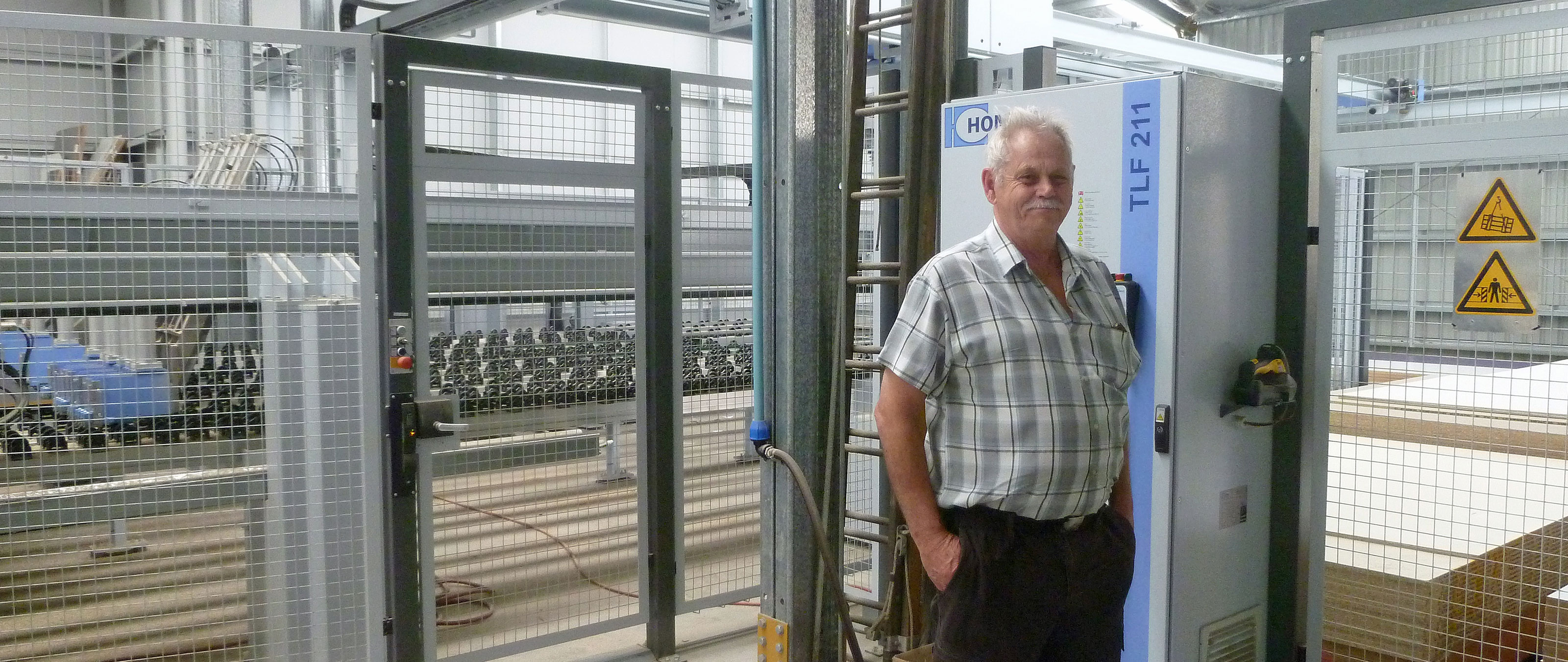
The article was first published in the AWISA Magazine, Summer edition 2016.
www.awisa.com
George is the owner of Kaiman Cabinets in Queensland and is very impressed of his latest investment which brought real value to his company.
“It’s an awesome combination that works absolutely harmoniously together delivering amazing productivity increases.” George likens the storage system to having your own personal genie working in the background silently handing you sheets exactly when you need them. “Watching it independently working away in the background gives you the sense the thing is alive and has a mind of its own. It’s the ducks guts”, he says.
Automation leads to rapid change
Kaiman’s automated warehousing system from HOMAG Australia was installed beginning of the year and has, since then, improved the whole production process for the Queensland company. George went on to recount the old days before the new system arrived in February this year.
“We’d been busy for quite a while and getting busier by the month. Our cutting day started at 2am and usually finished about 7pm. It was becoming very apparent an upgrade was in order. Of course the problem was what to upgrade, too. I‘d done quite a bit of research, walked the isles with those in the know, travelled overseas visiting factories and speaking with the very talented awe-inspiring people who conceive and perfect this sort of equipment. At the end of it all I decided on the HOMAG offer so went about doing a cost analysis and came to the conclusion the cost to me was more if I didn’t invest in the system.”
“You can’t be romantic about investing in technology”
George Kaiser and Peter Norman founded Kaiman Cabinets in 1979. Their cabinet genesis was in an old farm shed on George’s parent’s rural property. They started with a radial arm super saw, senco sn1 nail gun and an iron. A lot has changed since then. Today, they employ around 35 people and accommodate a 1600 square metre factory in Logan Village, which is about 45 kilometres south of Brisbane. It’s in George’s nature to continually challenge himself and research better ways and better systems.
“No matter how well you think you are placed I believe the quest for improvement should be ongoing. I fall in easy with technological change while initial costs have always been scary I can categorically state without exception each new investment along the way has resulted in a growth sprout.” George continues, “I approach it with the view that you can’t be romantic about investing in technology it needs to be researched thoroughly and if the argument is convincing then the time to upgrade is as soon as cash flow permits, any point past that time is costing your business dearly.”
A very flexible talent
HOMAG Australia has delivered more than 40 storage systems in Australia now, and it speaks for itself. In addition to managing the flow of panels the TLF 211 controls all stock automatically. All stock is documented in the system. The scanning of bar codes provides a quick integration of panels into the system. All offcuts albeit reduced because of the smart software is integrated in the storage and can be used which is very important in terms of overall manufacturing efficiency. Thanks to the seamless integration of software, Holzma’s Cut Rite talks to the TLF and they understand each other right away. The customer knows exactly what to order.
More output with HPP Power Concept
At the heart of the plant is the HPP saw. “The model HPP 300 comes with Power Concept and automatic labelling in the storage. It is a very compact machine. It’s a wolf in sheep’s clothing. It can achieve so many parts when they are needed,” explains HOMAG’s sales representative Mark Vowles.
Each cutting pattern is a cycle. Each cycle could be a book of four panels or an offcut. The sawyer does not need to wait and look for panels or misplaced boards; he just produces what is coming to him. Additionally, he doesn’t need to attach labels anymore which always used to slow down cutting jobs. Now it all happens together and automatically without waiting times and therefore, a huge volume of parts can be cut.
George is totally chuffed with the new storage system as he explains. “People ask how long before the pay back; I believe it already has paid back in the sense that although it saves about two men labour it also greases the system in as much as it allows much better control with a lot less effort but more importantly it has allowed us to take on new work which has become ongoing and the margins from that come close to payback. Not to mention, what monetary figure can be put on the removal of angst and peace of mind?”
“No matter how well you think you are placed I believe the quest for improvement should be ongoing.”George Kaiser, Managing Director, Kaiman Cabinets
About the company
George Kaiser and Peter Norman founded Kaiman Cabinets in 1979. Their cabinet genesis was in an old farm shed on George’s parent’s rural property. They started with a radial arm super saw, senco sn1 nail gun and an iron.