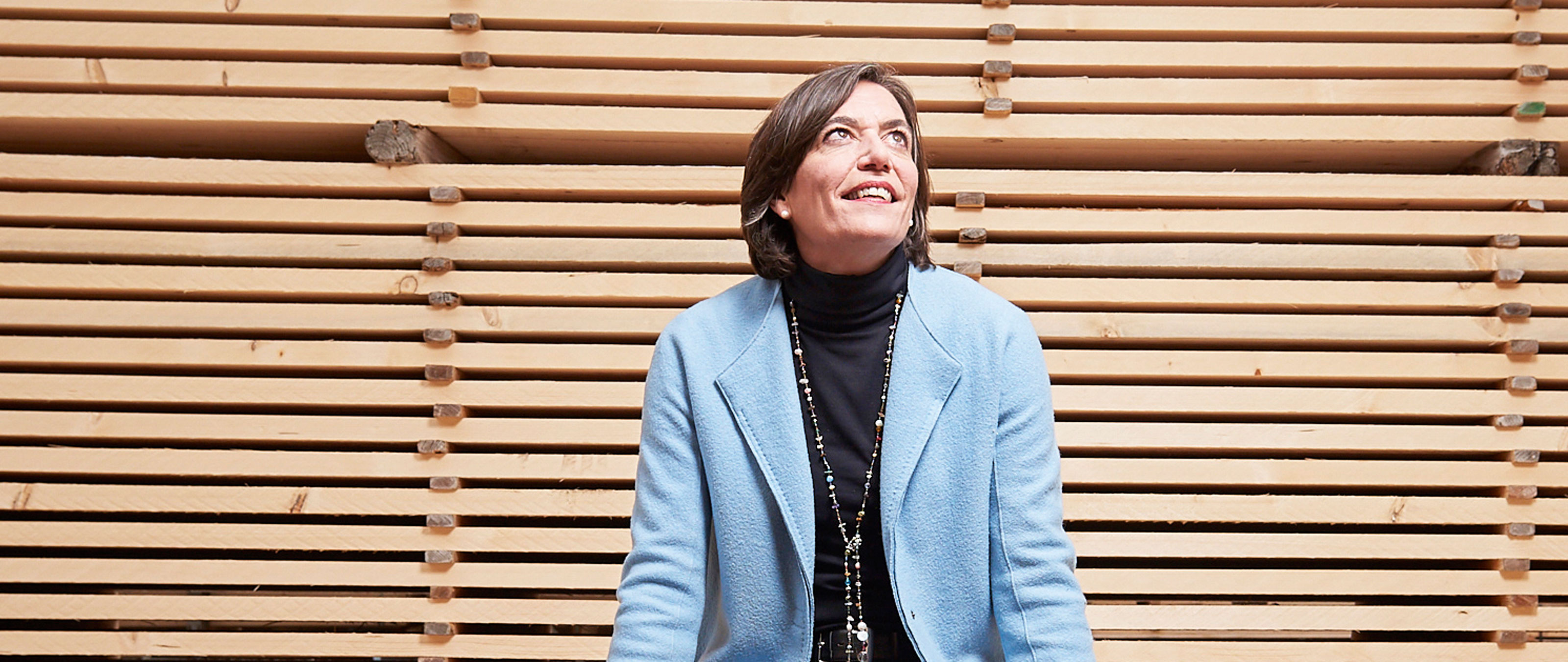
Trucks are maneuvering, machines are humming, the smell of spruce and fir is in the air. Visitors notice immediately: It’s all about wood at Blumer-Lehmann in Gossau, a town near St. Gallen, about 25 kilometers south of Lake Constance. Blumer-Lehmann belongs to the Swiss Lehmann Group and is one of the leading timber construction companies in the country. “We are convinced that wood is the building material of the future,” says Katharina Lehmann, who has been running the business for 24 years. When the boss talks about wood, she is completely in her element. “I grew up in the company,” she says. The business has been in her family for five generations. Her ancestors started out in 1875 with a sawmill on a creek; later roof trusses, then barns for agriculture were added to the portfolio. “For about 20 years, we have been constructing complete buildings made of wood, including apartment buildings, school buildings, office buildings and industrial buildings,” Lehmann says, adding: “We take care of every step of the process – from the felled tree to the finished house.” The portfolio not only comprises breathtaking free-form constructions like the Swatch headquarters in Biel or the Apple store in Bangkok. A large part of the business consists of comfortable buildings made of wooden modules. “We manufacture the complete modules individually in our factory according to the customer’s wishes,” says Lehmann – with digitally controlled plants that produce the elements quickly and efficiently.
Troubleshooting with digital eyes
The process begins at the timber stacks, where a crane clamps logs in its gripper and places them on a conveyor belt. The logs disappear into the sawmill where they are cut up. The boards are then stored in the drying chamber for three to four days. Houses must be stable. The wood used for them must be free from defects. Looking for individual knotholes, cracks or resin deposits and sawing them out takes far too long. “That is why we bought a machine sorting system in order to better refine the wood,” Lehmann says. The dried boards shoot through the planing machine on a conveyor belt. Watching over them are digital eyes, scanning the wood. Smart software detects errors immediately and reliably. But there is more: The machines from the Danish supplier System TM, which is part of the HOMAG Group, instantly saw out the flaws. The machine can eliminate more than seven defects per second. Another System TM machine immediately glues the parts together again. To this end, it cuts serrations into both ends of the board, which perfectly fit together like a lock and key. This so-called finger-jointing process thus produces standardized boards – ideal for use where maximum stability or aesthetics are required. In a further processing step, several of the pieces of wood joined together in this way are glued together in layers at right angles to the wood grain or nailed together in an environmentally friendly way with hard beechwood pins. This results in 20-centimeter-thick beams. Blumer Lehmann has this production step carried out by an external company.
Prefabricated panels and modules
The next step in the process chain is the prefabrication of the panels. Employees assemble the frame of a timber construction element from beams of different lengths and cover it with a sheathing. Then the WEINMANN multifunction bridge slides over the wall – and nails, drills, saws, mills, and marks. Within a few seconds, it fastens the panel and provides the openings for doors, windows and shafts. The semi-finished element is then turned and the cavities are filled with insulation material. A second sheathing closes the wall. After a short finishing process, the wall is automatically erected and then transported to the intermediate storage. The carpenters in the factory assemble walls, ceilings and floors into finished modules or pack them individually. Then the journey to the construction site by truck begins. With the help of a crane, the fitters will erect the prefabricated elements there. It takes two to three days for the complete building to be erected – an advantage especially in narrow inner cities or when things have to move quickly for customers, for example in hotel extensions. That is why Blumer Lehmann goes one step further. “We often deliver the individual modules already equipped with electrical wiring, water pipes, wallpaper, tiles and kitchen units,” says Lehmann. Suppliers commissioned by the company will take care of that while the modules are still in the factory. Making careful use of limited resources is very important for the company. Therefore, it ensures that nothing goes to waste. “We can only use about 60 percent of a complete tree in production,” Lehmann says. What remains is residual wood. The tour leads past two towers that look like silos. “This is where we store the wood pellets that are produced at our plant.” And what happens to the tree bark? That is also taken care of. It is shredded into mulch and goes into landscaping. Or it is processed into briquettes and, like the pellets, used in the company’s own power plant. An ecosystem in which nothing is thrown away.
Author: Heimo Fischer
An article from the customer magazine performance issue 20 | 2021 Find more information here.
“We take care of every step of the process – from the felled tree to the finished house.”Katharina Lehmann, Manager of Blumer Lehmann
Blumer Lehmann
Blumer Lehmann is located in Gossau, a town near St. Gallen, about 25 kilometers south of Lake Constance and belongs to the Swiss Lehmann Group. It is one of the leading timber construction companies in the country and specialised on free-form constructions, modular constructions and temporary buildings.
Find more information here.