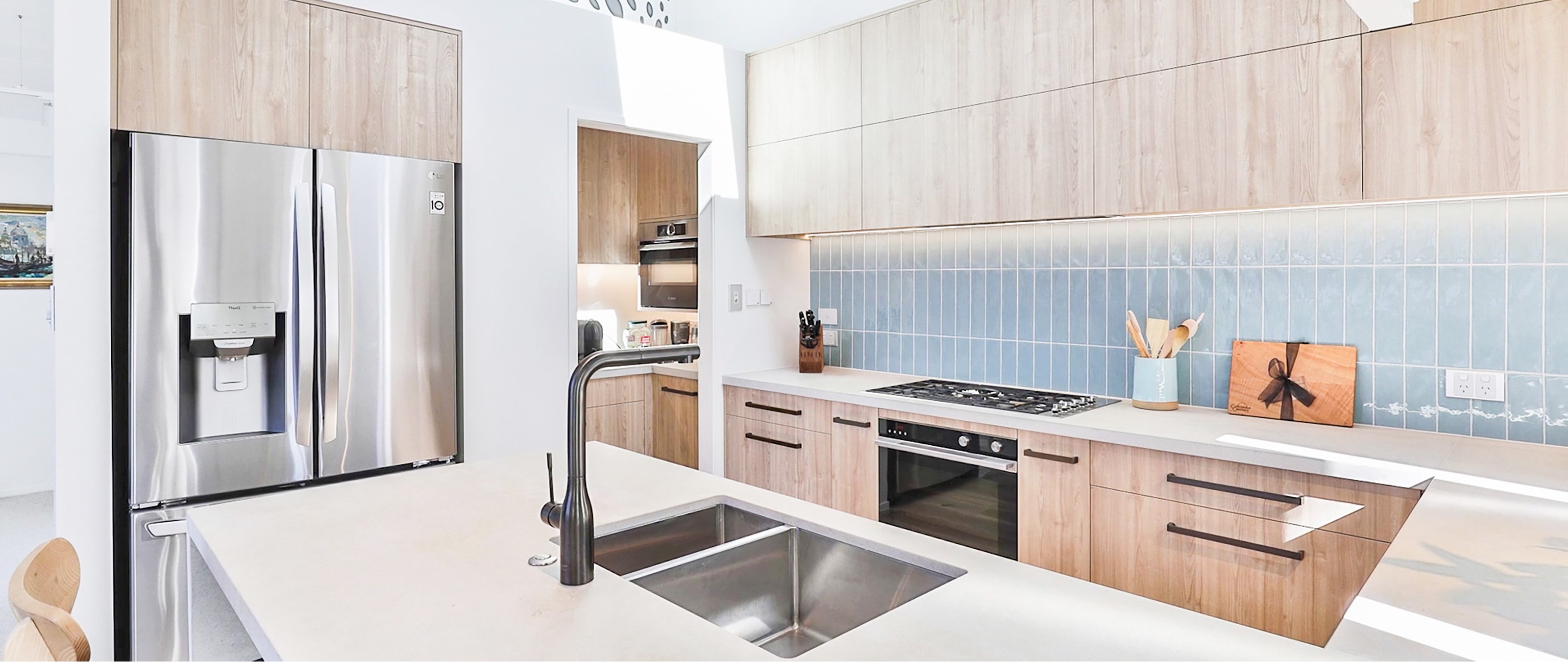
In 2011, what started as a singular ambition in the world of cabinetry has now flourished into Cutting Edge Cabinetry, a testament to the power of passion and precision craftsmanship under the stewardship of founder William Haveland. The Joinery, nestled in Pukekohe, south of Auckland, has cultivated a reputation for excellence, delivering products and services that embody quality and a distinctly personal touch.
Cutting Edge Cabinetry started out in 2011 as a one-man band and has now grown into a small but well-respected company committed to delivering a quality product, with a warm, personal service that you would expect from a small company.
Their team holds a deep passion for their craft, consistently aiming to meet the highest standards of craftsmanship. Satisfying customers and delivering durable products are among their top priorities. They are dedicated to continual learning and development, incorporating the latest design elements, hardware, and products as they become available, ensuring their clients receive the finest results.
William Haveland is the founder of Cutting Edge Cabinetry, a Joinery situated in Pukekohe, south of Auckland. Initially, Cutting Edge Cabinetry serviced local residents by creating custom kitchens, and concurrently, they provided commercial office fit-outs for various professional firms, including law and accounting practices. Over the years, they have maintained a diverse portfolio of residential and commercial projects.
Evolving with Precision and Passion
As business progressed, William’s team expanded, and approximately eight years ago, they relocated to their current premises. Currently, Cutting Edge Cabinetry employs a team of seven people. The Joinery concentrates on two primary areas of expertise: kitchen designs and installations for both home renovations and new constructions in collaborations with builders, and the commercial side of the business, which, while inclusive of kitchen projects, extends to crafting feature walls, reception desks, and general interior furnishings for properties.
William Haveland made a strategic decision to invest in a HOMAG edge bander, a choice influenced by previous positive experiences with this brand of machinery. His familiarity with HOMAG stemmed from his time at an earlier company, which boasted two robust HOMAG machines. Seeking an upgrade from his initial setup, Haveland acquired a HOMAG edge bander Optimat machine that significantly occupied his first workshop’s space, but importantly delivered a higher quality product. However, as demand increased and the need to stay current with technology arose, Haveland aimed for efficiency upgrades, particularly transitioning to laser edge technology to streamline processes and reduce the time staff spent on post-production cleanup. William Haveland: “Each year we try and invest in newer machinery to increase the quality and the efficiency of what we’re producing and develop the work that we’re doing.”
The team at Cutting Edge Cabinetry explored various brands and options before selecting their new edge bander. Opting for HOMAG once again, they purchased the EDGETEQ S-200 model, which suited their needs without reaching the higher pricing tiers of edge banders. This particular machine includes the airTec option, which allows the use of a single glue tank and facilitates the processing of all their carcass board with laser technology, as well as their colored materials, when available.
Another reason for their choice was the EDGETEQ S-200’s pre-milling heads. Though their materials already come from the CNC, having the ability to pre-mill ensures a clean, finished edge before applying the edge banding. This is especially useful when cutting to final size, either when trimming off excess edge banding or when cutting on the dimension saw.
Embracing Enhanced Efficiency with HOMAG’s edge bander EDGETEQ S-200
William Haveland values German engineering for its precision, which is particularly important for his need for a stable and well-crafted machine to achieve refined results. Transitioning to the new machine was fairly smooth; their old machine was removed in the morning, and the new one was installed by the afternoon.
Due to the brand consistency, the interior mechanics of the new machine were similar to those of the older model, even with the new model being years newer.
The EDGETEQ S-200 is user-friendly with its small intuitive touch panel, simplifying the loading of programs. After setting up all the preset programs and with pneumatic adjustments incorporated within the machine, manual tweaking became minimal. The team found that they could essentially just turn it on and begin using it immediately.
Initially apprehensive about transitioning to a significantly smaller HOMAG machine, William Haveland found the EDGETEQ S-200 airTec to not only meet but exceed their expectations for their operations. Despite concerns about the investment, the technical capabilities of the EDGETEQ S-200 proved to be perfectly aligned with their needs of Cutting Edge Cabinetry. Although their previous, larger machine operated at a faster feed rate, the compact design of the EDGETEQ S-200 offered unexpected efficiencies. Its shorter run distance allowed for quicker, tighter spacing between panels, resulting in a higher throughput than was possible with the larger machine. This efficiency gain, coupled with the bonus of additional workshop space and extended outfeed table room, marked a significant improvement in their production process.
The edge finishing capabilities of the EDGETEQ S-200, notably its glue line and radius scrapers, required minimal adjustment and facilitated the processing of multiple finishes without the need for subsequent manual clean-up. This efficiency is particularly beneficial in a workshop environment like Cutting Edge Cabinetry’s, where the demand for switching edge tapes for different kitchen projects is high. The variability in colors and finishes from one kitchen to the next is necessitated a machine that could adapt quickly without the constant need to switch glue pots, ultimately saving time and justifying the investment in higher-priced edge tape for the sake of superior finish provided by the airTec technology.
Demonstrating the capabilities and finishes of their edge tape to customers in their showroom, Cutting Edge Cabinetry ensures that their clients understand the quality of the product before purchase. The team’s own critical eye towards the edge tape finish they produce underscores their commitment to a high-quality output, recognizing their deep understanding of the machine’s capabilities and desired consistency in their products.
From Concept to Completion
When clients approach Cutting Edge Cabinetry with the intention of redesigning a kitchen, the process begins with gathering photos of the existing space. Back in the office, these visuals are transformed into a new, three-dimensional design using specialized software, enabling clients to review plans and designs. The selection of colors takes place in the showroom, where clients can visualize their options. Following a client’s commitment, Cutting Edge Cabinetry conducts a detailed site measurement and then proceeds to draft the design using Computer-Aided Design (CAD) software, which directly communicates with their Computer Numerical Control (CNC) machinery.
The preparation stage involves creating comprehensive working drawings that not only guide the fabrication process but also assist clients in understanding necessary modifications to plumbing and electrical layouts. These drawings are then fed into the CNC machine through an optimizer, ensuring efficient material usage. Each component is meticulously cut, labeled, and prepared with specific instructions for edging and any special requirements highlighted.
Assembly is an in-house operation, where each job is assembled and rigorously tested to confirm that all pieces function correctly and meet the spatial requirements of the room they’re designed for. This careful attention to detail secures a seamless fit during installation.
By managing all aspects of the fabrication and assembly within their facility and conducting thorough pre-installation testing, they significantly streamline the installation process. This approach not only minimizes the duration of installations within clients’ homes but also reduces transportation time, exemplifying their commitment to efficiency and customer satisfaction.
Over the years, Cutting Edge Cabinetry has completed a number of impressive projects. Each project that pushed the limits of their capacity, scale, and technical capabilities has fostered growth and been rewarding for the company.
Cutting Edge Cabinetry’s commitment to refining and enhancing operational efficiencies and process streamlining stands at the core of their objectives, driving their pursuit of excellence and innovation in the field.
Videos
Please confirm that when you use YouTube, data such as your IP address, browser identifier and similar may be transmitted to Google.
» Privacy Policy
From vision to excellence: Cutting Edge Cabinetry saves a lot of time and gets a better finish by using the HOMAG EDGETEQ S-200 with airTec. The joinery concentrates on two primary areas of expertise: kitchen designs and installations for both home renovations and new constructions in collaborations with builders, and the commercial side of the business, which, while inclusive of kitchen projects, extends to crafting feature walls, reception desks, and general interior furnishings for properties.
“For a smaller workshop where we’re swapping edge tapes quite a lot - we run one kitchen and the next kitchen is a different color. The carcass is a different color than the doors. We’re running different finishes, sometimes multiple colors on one job. Being able to switch colors quickly without changing the glue pot in and out all of the time. That’s saving us quite a lot of time. Plus, we’re getting a better finish off the airTec.”William Haveland, Owner Cutting Edge Cabinetry
No job is too big or too small for Cutting Edge Cabinetry.
Just as our name suggests, we aim to be one of the leading kitchen cabinetry businesses in Pukekohe and the greater Auckland and Waikato regions. We pride ourselves on our exceptional design, workmanship and attention to detail. We use quality hardware and materials from reputable brands to ensure that the finished product not only looks great but will stand the test of time.
Cutting Edge Cabinetry