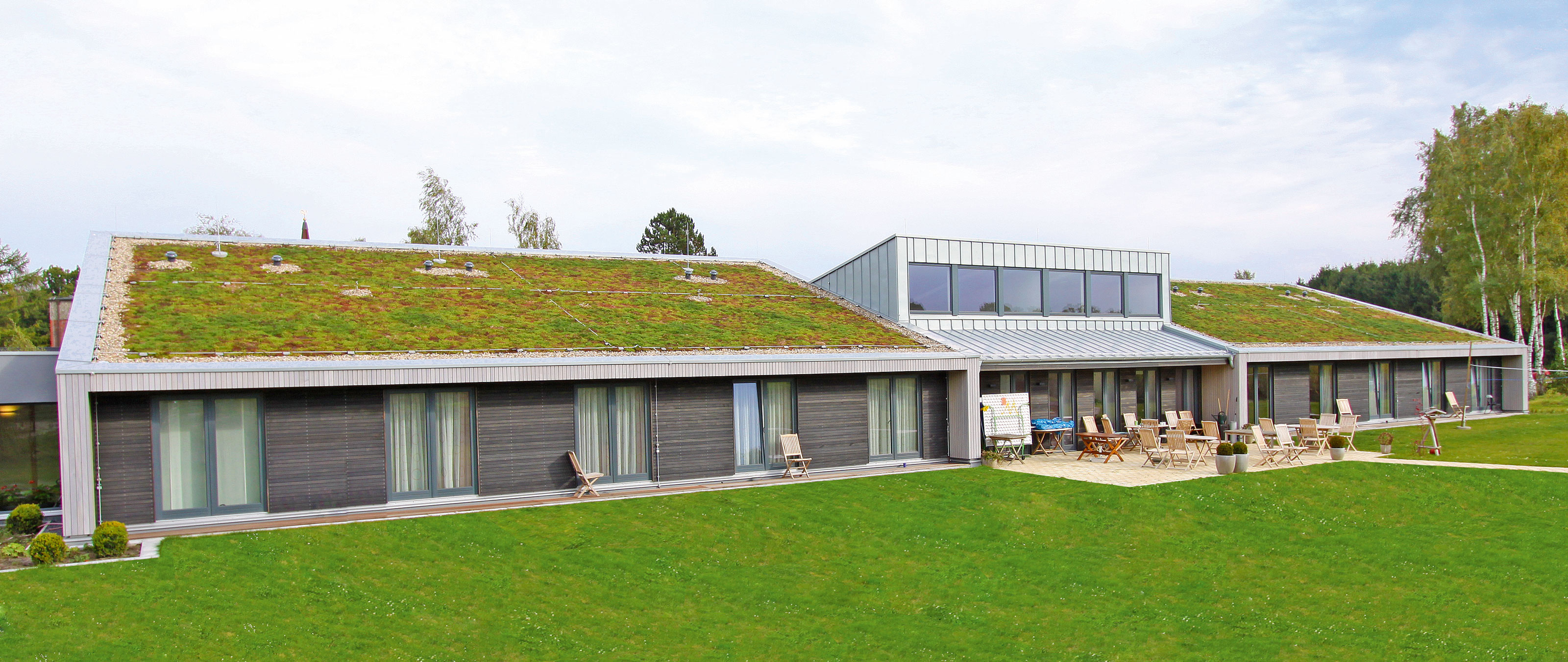
Au cours des deux dernières étapes de sa croissance, elle a mis en place une automatisation complète de la production, ce qui lui a servi de tremplin vers l'avenir numérique. Dans le domaine de la construction bois, tout repose sur la croissance : c'est la seule manière de garantir l'augmentation rapide du volume des commandes, de maintenir ou même d'améliorer sa position sur le marché tout en minimisant le risque de hausse des prix des matériaux en cas de carnets de commandes pleins. D'autre part, de plus en plus de voix se font entendre pour exprimer leur crainte d'une éventuelle baisse des commandes en raison de la crise du coronavirus qui se poursuit. Certes, au vu de la situation actuelle, la construction massive traditionnelle sera probablement la plus touchée, mais une certaine attention ne peut pas nuire. Dans ce contexte, une croissance modulaire, progressivement orientée sur le volume des commandes existantes, permettant une adaptation à la situation du marché grâce à des étapes d'investissement raisonnables, tout en s'inspirant d'un esprit d'entreprise visionnaire, apparaît comme une approche sensée. En effet, il est judicieux de bâtir les fondations des développements de demain avec l'investissement d'aujourd'hui.
Une quantité de pièces décuplée
L'entreprise de charpentes Hamdorf, basée dans le Land du Schleswig-Holstein, constitue un bon exemple de cette croissance progressive. Son objectif principal concerne la construction d'objets et de bâtiments commerciaux et la fabrication d'éléments d'ossature en bois pour d'autres entreprises de charpentes de plus petite taille. De plus, forte de ses 46 employés, l'entreprise fabrique et monte des connecteurs métalliques, couvre les toits et est également active dans la construction de façades. Cela fait maintenant une bonne dizaine d'années que Daniel Hamdorf, directeur général, a été confronté pour la première fois à ses limites en termes de capacité de fabrication d'éléments d'ossature bois. Il produisait à cette époque environ six maisons en bois par an, et bien que l'on se soit retrouvé en 2009 au beau milieu de la crise financière, et pas nécessairement dans un pays traditionnel de la construction bois, la demande de produits dans ce secteur a fortement augmenté. Pour pouvoir profiter de cette reprise, Hamdorf a construit un nouveau hall de production et investi dans une installation à trois tables de WEINMANN. Une table de travail WEINMANN déjà présente a été incluse dans la nouvelle ligne de production pour servir à la production des ossatures bois, et un peu plus tard, une cinquième a même été ajoutée. Elle servait de table tampon et était aussi dédiée à des usinages spéciaux tels que les façades. Finalement, la nouvelle ligne de production a permis à l'entreprise de charpentes de multiplier par dix sa capacité de construction bois pour passer à 60 maisons par an ou un équivalent correspondant en éléments par m2. C'est ainsi que l'on a réussi à s'en sortir sur le site de Fahrenkrug jusqu'à 2019 environ. A cette époque, et malgré l'introduction d'un fonctionnement en deux équipes ayant permis d'augmenter le nombre de maisons à environ 100 par an, on avait à nouveau atteint les limites de la croissance. « Je pense que nous avons acquis une bonne réputation dans la région grâce à un grand nombre de projets réalisés par nous-mêmes et par nos clients de la construction bois », explique Daniel Hamdorf pour éclairer son succès. « A cela s'ajoute le fait que la construction bois, avec ses normes de qualité élevées et un bon bilan carbone, est de plus en plus tendance, même dans le Nord. C'est la raison pour laquelle elle est aujourd'hui une méthode de construction bien établie auprès des clients privés et professionnels. »
Une extension modulaire
Au vu du bon développement de l'entreprise, Daniel Hamdorf a envisagé en 2020 une autre mise à niveau pour la fabrication d'ossatures bois. Après avoir consulté les employés en charge de la préparation du travail et de la production, il a tout d'abord pensé à l'automatisation du processus d'isolation : « C'était la première étape. Nous souhaitions par ailleurs continuer à optimiser le déroulement de la production. Ainsi, nous voulions à nouveau réduire le fonctionnement à deux équipes qui était en place depuis trois à quatre ans à une seule équipe – tout en conservant la même cadence de production, voire en l'augmentant ». Avec ce concept, Daniel Hamdorf a demandé conseil à WEINMANN et a mis en œuvre, en concertation avec le chef de projet Jörg Groß, une ligne de production sur mesure. Elle se compose de cinq tables qui, contrairement à la variante précédente, au-dessus desquelles passent des ponts multifonctions. Deux de ces ponts sont nouveaux : un WALLTEQ M-310 WEINMANN insuFill permet, d'après D. Hamdorf, d'économiser 80 % de temps de travail dans ce domaine grâce au soufflage entièrement automatique des matériaux isolants, et un WALLTEQ M-120 prend en charge l'usinage des revêtements sur les deux tables avant. Sur les deux tables arrière, le pont multifonctions de l'ancienne installation à trois tables remplit ses fonctions à l'aide d'un nouveau logiciel. Les tables existantes ont également été largement modernisées. Elles ont par exemple été équipées de transports longitudinaux qui permettent une commande centralisée du flux de travail à long terme (voir ci-dessous). Les deux tables les plus anciennes ont été remplacées par de nouvelles acquisitions et offrent aujourd'hui encore de bons services dans la fabrication séparée d'éléments de plafond. Daniel Hamdorf a été particulièrement impressionné par la façon dont « les unités de production existantes ont pu être parfaitement intégrées à la nouvelle ligne. Je n'avais pas prévu que le logiciel actuel fonctionnerait encore sur notre pont qui n'est plus tout jeune. Ici et sur les tables, on a très clairement vu que les possibilités d'extension modulaires des machines WEINMANN ne sont pas une simple promesse publicitaire ». Même au niveau de la périphérie de l'installation, des ajustements ont été effectués afin d'optimiser le flux de matériaux autour de la fabrication. Entretemps, chaque table est desservie par un dispositif de levage pour panneaux à l'exception de la station d'isolation, de sorte que le matériau puisse être posé rapidement sur quatre stations et usiné par un pont multifonctions. Ceci peut être fait en même temps pour le revêtement intérieur et extérieur et, en alternance, sur les deux tables assignées, sans longs temps d'arrêt du pont. Ce parallélisme de plusieurs opérations explique, en combinaison avec les temps d'usinage fortement réduits au niveau de la station d'isolation, le rendement nettement plus élevé de la nouvelle ligne.
Penser à l'avenir
En investissant dans un poste de gestion de la production Granit MES, Daniel Hamdorf a encore exploité un autre potentiel pour augmenter les quantités produites. « Pour moi, Granit était avant tout synonyme de cloisons multiples », affirme le maître charpentier pour justifier cet investissement. « Il existe certainement d'autres solutions, mais si l'on y regarde de plus près, celles-ci sont toujours sources de problèmes ». L'avantage principal des cloisons multiples réside dans le raccourcissement des cycles de travail : « Lorsque je rassemble trois ou quatre cloisons intérieures plus courtes en une cloison multiple, je n'ai plus besoin de les synchroniser individuellement, elles traversent la ligne de production en un seul cycle de travail », explique Jörg Groß, chef de projet chez WEINMANN. « Je gagne également du temps lors de la préparation et de l'assemblage des éléments de charpente, car la cloison multiple dispose d'une membrure supérieure et inférieure continue. Si un tel système est bien mis en place, on obtient jusqu'à 20 ou 25 pour cent de puissance d'une ligne de production en plus, en fonction de la longueur moyenne de la cloison. Cet effet est particulièrement évident dans le cas de grands projets avec des composants qui se répètent. C'est également ce qui rend Granit intéressant pour les entreprises pour lesquelles le bénéfice d'autres modules du logiciel est plutôt facile à gérer ». Bien sûr, l'aspect visionnaire est également à prendre en compte. Dans cette optique, il est essentiel que les entreprises de charpentes se lancent dès aujourd'hui avec le nouveau logiciel afin de se familiariser avec le système. Si les quantités de pièces continuent ensuite à augmenter, elles connaissent déjà la procédure et tout stress est alors évité pour l'apprendre. C'est également ce que pense Daniel Hamdorf : « Notre entreprise a connu une croissance constante au fil des décennies, car notre devise est de réinvestir une bonne partie des bénéfices. Mon grand-père lui-même était parti de rien ou presque avant de passer le flambeau et de transmettre une entreprise de charpentes bien équipée, et j'ai aussi toujours à l'esprit l'avenir de mes enfants lorsque j'investis. Et, au vu de la situation, il se pourrait bien qu'il passe par un agrandissement de l'entreprise de charpentes Hamdorf. En termes de terrain, nous avons encore beaucoup de place pour de nouveaux halls, et un poste de gestion de la production centralisé pourrait s'avérer très intéressant ». Par ailleurs, Granit fait déjà partie aujourd'hui d'un processus de numérisation complet qui permet de se préparer pour les défis à venir sur le site de Fahrenkrug. Cela implique d'unifier la multitude de solutions logicielles de l'entreprise ou de les mettre en réseau via des interfaces, «de manière à créer un processus numérique homogène dans l'entreprise, qui couvre chaque projet et est accessible à tous les employés. Granit sera l'interface de fabrication dans ce processus. »
Artisanat 4.0
Donc l'industrie 4.0 ? Sur le principe oui, mais pour toutes les opérations d'automatisation et de numérisation, l'entreprise de charpentes Hamdorf souhaite rester une entreprise artisanale. En premier lieu, on ne propose pas de solutions standard aux clients, mais on leur livre ce qu'ils souhaitent. Dans la fabrication, cela concerne, par exemple, la structure de cloison variable et les matériaux utilisés – la nouvelle ligne permet ici une installation très flexible. « Cela est évidemment également important dans le domaine de la fabrication à façon », explique Daniel Hamdorf. « Un charpentier nous transmet un bon pourcentage de sa valeur ajoutée et nous fait confiance lorsqu'il commande ses éléments chez nous. Je peux également lui charger les cloisons, ce qui est optimal pour lui, et lui offrir un petit plus décisif au niveau du SAV qui nous démarquera de la concurrence. Ici et dans les autres domaines, notre objectif doit être le suivant : le client acceptera peut-être de payer un peu plus cher, car il accorde une grande valeur à notre petit plus en termes d'individualité et de sécurité ». Sur le thème de la sécurité, on peut ajouter le fait que la numérisation et le contrôle de la production entraîneront également une meilleure planification de la production, avec tous les effets secondaires positifs, notamment une sécurité de calcul encore plus élevée et une livraison précise des pièces de construction, pour laquelle on note encore aujourd'hui un écart de ±5-6 jours. En attendant, il reste encore quelques petits problèmes à résoudre sur le site de Fahrenkrug, mais la première étape a été franchie : « Après une phase de transition toute en douceur, nous avons pu rapidement ramener la fabrication à une seule équipe de travail », explique Daniel Hamdorf. « Depuis lors, nous fabriquons le même nombre d'éléments avec quatre employés qu'auparavant avec deux équipes de trois. Pour la première fois, nous avons noté une réduction des coûts de l'installation, et grâce à l'utilisation de Granit, le nombre de pièces que nous produisons va prochainement augmenter encore un peu plus. A long terme, la ligne de production nous offre la possibilité de doubler le nombre de pièces que nous produisions jusqu'à présent en fonctionnement avec deux équipes, si la demande continue d'augmenter. Notre objectif est donc de 200 maisons par an. »
Texte: Dr. Joachim Mohr
Un article du magazine spécialisé mikado, édition juillet/août 2021 Pour plus d'informations, cliquez ici.
« J'ai été particulièrement impressionné par la manière dont les unités de production existantes ont pu être parfaitement intégrées à la nouvelle ligne. »Daniel Hamdorf, directeur général Zimmerei Hamdorf
Zimmerei Hamdorf
Située à Fahrenkrug, dans le Schleswig-Holstein, l'entreprise de charpentes Hamdorf a pour objectif principal la construction d'objets et de bâtiments commerciaux et la fabrication d'éléments d'ossature en bois pour d'autres entreprises de charpentes de plus petite taille. De plus, forte de ses 46 employés, l'entreprise fabrique et monte des connecteurs métalliques, couvre les toits et est également active dans la construction de façades.
Website