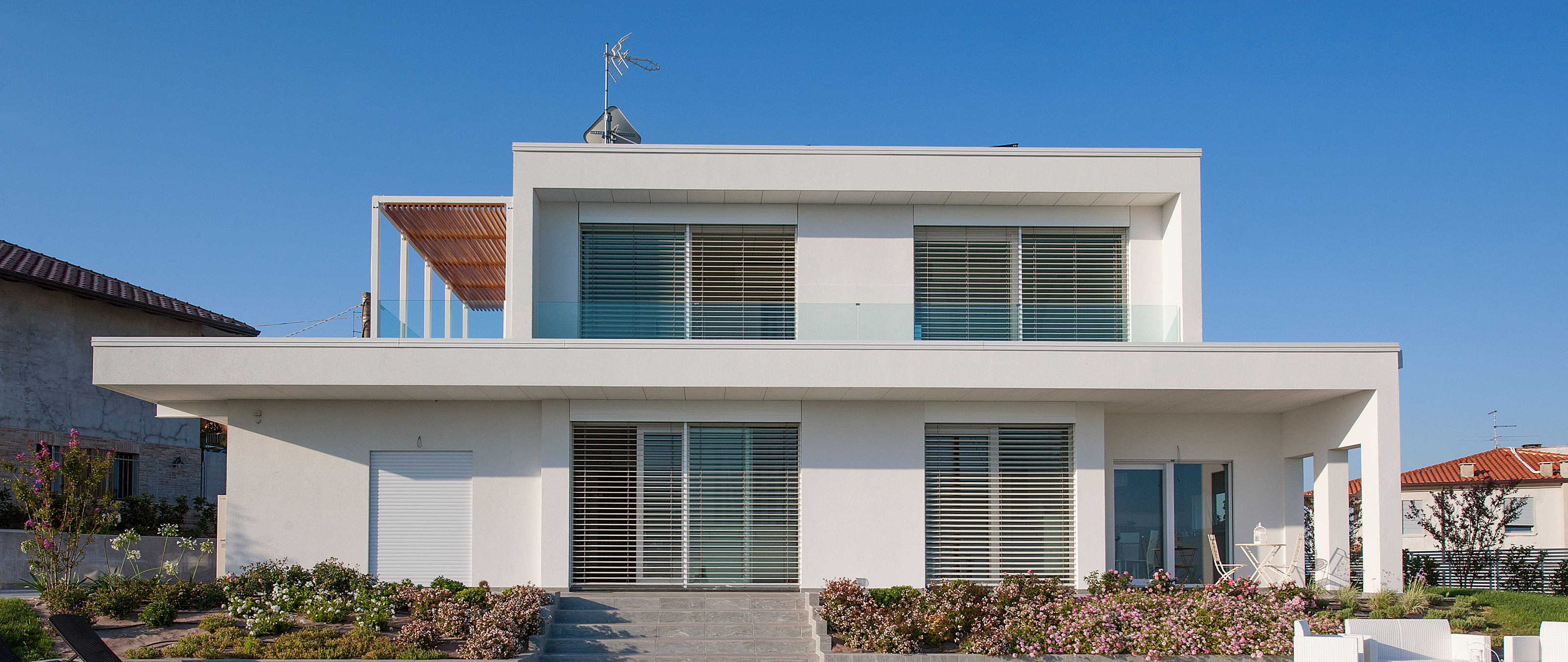
Subissati is a company based in Ostra Vetere, Italy. Founded in 1963, it currently employees around 50 people. It is a family-run business and the managing director is Paolo Subissati. Subissati produces around 100 timber frame and CLT objects annually, including houses and commercial buildings such as schools. Most of the buildings are supplied to the Marche, Tuscany and Romagna regions of Italy. The company site is spread over a total of 40,000 m² and includes two production facilities and an administration building. One production facility is used for painting work, while the other is used for the entire timber work process. All the raw timber required for timber frame construction is impregnated with organic salts in an autoclave. The houses are designed individually according to customer requirements; 90% are timber frame constructions, and the remaining 10% are CLT constructions.
Subissati had already automated its production in 2012 and invested in the appropriate technology. To make production flexible and fit for the future, the company decided to purchase a WEINMANN compact line, consisting of a WALLTEQ M-380 multifunction bridge (formerly known as the WMS 150) and a butterfly turning table. They also purchased an insert table and a setup and distribution trolley, and use the compact line to produce all of the wall elements. To shorten throughput times, the frame work is created on an insert table and then transported to the subsequent work table, where the first element side is closed. The planking is attached using the CNC-controlled multifunction bridge. Depending on the wall type, a further internal planking layer may also be attached to the OSB panel. The cut-outs for electrical wires and pipes are created in this layer. The element is then turned. The entire turning operation is performed using the two adjustable assembly tables. Once the element has been turned, all installations and the insulation are fitted in the element so that the second element side can then be closed with a further OSB panel. The final part of the process is the external plaster-base sheeting, which is also attached and processed fully automatically with the WALLTEQ M-380.
The element, which is closed on both sides, is transported horizontally to the subsequent setup and distribution trolley, which is then used to set the element up. The element is then transported to the subsequent wall slot. In the wall slot, windows are installed where required and the elements are made ready for transport.
As a special highlight, the plant has been designed to also allow all CLT elements to be processed on it. For this purpose, the assembly table is fitted with wear plates that can be raised. If CLT elements are to be processed, the elements are placed on these plates. This means that the multifunction bridge can perform all types of processing fully automatically, whether it's sawing, trimming, or drilling.
Using this type of production plant allows Subissati to achieve a very high level of prefabrication during production. The elements are delivered to the construction site completely finished - they just need to be assembled on site. Only the roof and ceiling elements are produced in the traditional way at the construction site.
Thanks to the production plant, Subissati has already produced around 500 houses and 30 schools since 2012. Paolo Subissati is seeing an increasing trend for timber construction in Italy and has a positive view when it comes to further development. Therefore, he recently decided to increase production capacities and the level of prefabrication even further. Again, Subissati opted for WEINMANN technology. Paolo Subissati: "Of all the manufacturers, WEINMANN has the most convincing concept. Their many years of experience and the option to extend all machines on a modular basis are ideal for us. We are very satisfied with the work that WEINMANN has done and with our excellent collaboration."
The existing plant will be extended by adding two further work tables and another WALLTEQ M-380 multifunction bridge. The extension means that the internal sides can now be processed independently of the external sides on the existing plant; the external sides will be produced using the new plant. The additional capacity will reduce the overall production time and significantly increase production capacity. In the future, Subissati will be able to produce up to 200 houses per year.
Source images: Subissati
An article from Holzzentralblatt, No. 17 from 27.04.2018. Here you can read the article.
“Of all the manufacturers, WEINMANN has the most convincing concept. Their many years of experience and the option to extend all machines on a modular basis are ideal for us. We are very satisfied with the work that WEINMANN has done and with our excellent collaboration.”Paolo Subissati, CEO