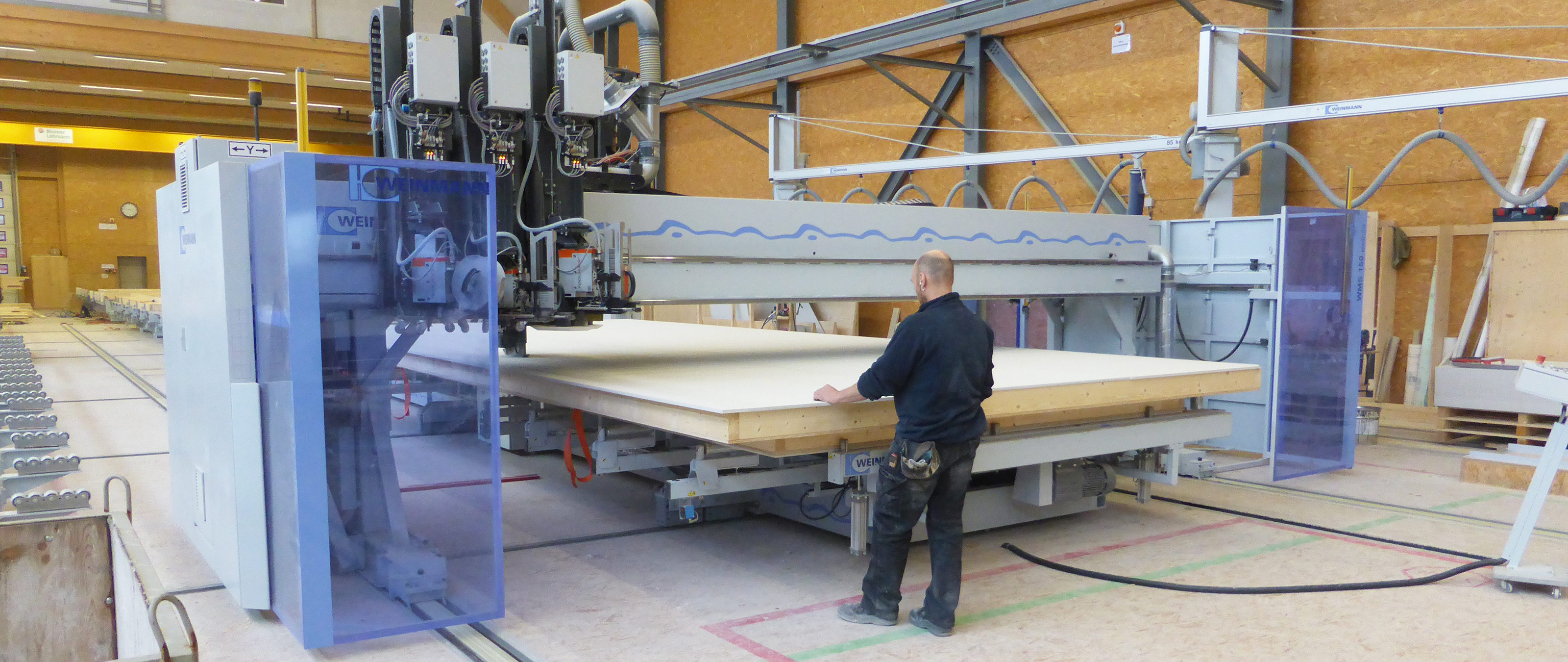
Not just temporary
Known for its numerous innovative ideas in the timber construction industry, Swiss-based Blumer-Lehmann AG is also one of the pioneers of modular timber construction. Today, even developers who are looking for a permanent solution are interested in its high-quality modular buildings, which are built using timber frame constructions that the company produces on a modern, automated production line.
One of the construction methods that timber work seems almost predestined for is modular construction. Strictly speaking, this form of construction-which some decades ago was mocked as "container construction"-actually represents exercising the potential of central timber construction principles when you consider that the fully completed modules allow up to 90 percent prefabrication. Contractors looking to construct temporary buildings are not the only ones attracted to the level of quality.
Diversity within a limited market
Blumer-Lehmann AG, based in Gossau, was one of the first companies in Switzerland to get involved in modular construction, entering the market segment over 20 years ago. According to General Manager Richard Jussel, the company has continued to develop its modular construction products ever since. As a Swiss company, it is active in a market containing several highly productive competitors, many of whom have undergone significant expansions in recent years. They are competing for a domestic order volume that varies by region and is limited by both the size of the country and its geographical features. One of the strategies that Blumer-Lehmann is employing in response to this market situation is involving itself in several of its sectors. In Gossau, for example, the company operates a saw and planing mill, a separate pelletizing plant, and a power plant, as well as being engaged in the construction of salt silos on an industrial scale. When it comes to timber work, the company does not only produce modular constructions - it is also active in traditional residential and commercial construction using timber elements, as well as conversion and renovation, turnkey construction, agricultural building construction, and large-scale timber construction of multistory buildings or housing developments. In all of these areas, the focus is always on timber frame construction. The company also uses innovative construction techniques in the area of free-form construction, and timber connections that do not contain metal for the construction of multistory buildings. In recent years, the company has been the subject of international attention in multiple areas thanks to their innovative projects. Well-known examples include the seven-story Tamedia office building in Zürich, which was built using timber connections containing no metal; or the Hotel Säntispark, the first four-story timber hotel building in the canton of St. Gallen. At present, Blumer-Lehmann AG employs around 300 people.
Modular construction 1: Temporary buildings
Modular construction makes up approximately 30 percent of the production volume in Gossau. This equates to a quantity of approximately 2500-3000 elements per year, and a sales share of 25-30 percent. At Blumer-Lehmann, the focus is usually on high-quality modular timber frame construction elements - even though these are in the upper price segment. "On the one hand, we represent a timber construction culture in which the carpenter assumes the responsibility for the construction of the entire wall," explains General Manager Richard Jussel. "On the other hand, in our opinion, timber frame constructions use wood in a particularly sustainable way." One of the elements that demonstrate the company's demand for premium quality is the high-grade sealing system between the modules. For this reason, the Swiss company offers a blower door test on finished buildings as one of their standard services. The company also checks interior air quality, with the targets being the values set by the "Gesundes Wohnen" [healthy living] label of the eco-INSTITUT. With this background, it goes without saying that all modular constructions produced by Blumer-Lehmann will meet high energy efficiency standards. According to Richard Jussel, contractors of temporary buildings are also impressed by this level of quality - especially when the building in question is a school or an office block. Examples for demand for this type of building include when an old school or office block is being renovated or optimized in terms of energy efficiency and will then be occupied again afterwards, or if the construction of a new residential development requires a rapid increase in school capacity but a new building will not be completed for several years - because of a long-winded approval procedure, for example. Therefore a temporary solution can end up being used for many years. The advantage of modular buildings in such situations is that they can be set up and put into operation at the desired location within a short time. Once they are no longer required, they can also be moved to another location just as quickly. This enables school authorities to use the building multiple times, whereas a private contractor would probably sell the building once it had been used. When these aspects are taken into consideration, there are substantial arguments for the quality claims of Blumer-Lehmann. Richard Jussel states: "On the one hand, you really cannot provide a healthy, comfortable learning or working environment with the almost unbearable room temperatures you find in shipping container architecture. Therefore, if the temporary building is required for a longer period of time, it is definitely worth using a high-quality timber construction, as this will result in better learning success and work results. However, there is another advantage for our customers: we offer them a tried-and-tested, high-quality end-to-end construction system that does not lose its value after use. This means our modular buildings can be reused over a long period without any compromises - which pays off for both public contractors, as it ensures a longer service life, and private contractors, as the resale value will be increased."
Modular construction 2: Series construction
With this background, it is no wonder that the modular buildings produced by Blumer-Lehmann AG have long since exceeded temporary status. Ultimately, they also offer contractors of permanent solutions a whole range of benefits, making them seem an attractive alternative to conventional forms of construction.
These benefits include a wide spectrum of potential time benefits, including:
- A short planning and approval phase thanks to a high level of standardization
- Shorter processing times as the building can be produced on the construction site at the same time as the preliminary work - Completion of a building on site in two to three weeks with low adverse impact on the environment of the construction site and without interruptions due to bad weather
- Ultimately, a high level of security in terms of the deadline and costs, resulting partially from the factors mentioned above
A degree of prefabrication exceeding the possibilities of conventional timber construction provides extra advantages:
- High-quality detail and precision when it comes to the room modules. These are produced by experienced teams using modern production systems under industrial conditions - and the same method is used for interior fittings and finishing
- A high standard for complex building installations that are planned in the work preparation and integrated into the module assembly
These are all advantages that make the high-quality modular construction seem the ideal solution, even for permanent projects with a tight schedule or limited construction site conditions, for example in urban construction, where the stress on the environment around the construction site is a key factor. Modular construction also demonstrates its benefits in buildings with a high level of technical installation difficulty or serial structures, for example complex office buildings, clinics and laboratories. In addition to this, it allows the timber construction company additional synergy effects in serial construction: Richard Jussel cites hotels or retirement homes as typical examples for this sector. Implementing this type of modular building technique allows the timber construction company to achieve a high level of manageable value creation in its own assembly facility: "For such projects, we work with experienced teams of window manufacturers, painters and plasterers, as well as sanitary, heating, and electrical engineers," explains Richard Jussel. "All these teams work efficiently at the same assembly location and thereby benefit from additional synergy effects that arise from the high level of standardization in series construction."
A modern production technique with optimized logistics
The quantities in modular construction alone make it understandable that in 2013, the Swiss company invested in new facilities and a highly automated production line. If we extrapolate the entire production volume based on the data for modular construction, there is no alternative to industrial production: on this basis, 7500 to 9000 elements pass through the production line in Gossau each year. In line with its focus, the company equipped the new facilities with a production system for timber frame elements. As the company already had a sizeable workload, the management team was not primarily interested in increasing quantities - it was more interested in achieving a consistently high level of quality and a clearly structured production sequence. The latter also benefits the quality, as a well-planned, clearly structured production process also increases the efficiency of quality management. The company also wanted to modernize its production in terms of employee satisfaction, as production was previously manual and took place in a tight space. In parallel to the new installation in production, the company made the individual modules and elements more uniform. According to General Manager Richard Jussel, "Automated production is not the sole answer to making production faster. To utilize potential to the full extent, a company also has to optimize its processes and products." This includes well-planned material logistics for the production line: the hall layout designed by WEINMANN therefore placed great importance on short routes between the material depots and work tables, fast and ergonomic handling systems, and providing sufficient space for transporting material in and out without any problems.
Flexibility and short response times
A WMS 150 multifunction bridge and five work tables form the core of the WEINMANN production system in Gossau. This production system is tailored to the quantities that the company produces and the wide range of business fields that it serves: it is used not only for wall, roof, and ceiling elements for conventional timber buildings and modular construction projects, but also for special components and facade elements for hybrid buildings. Order peaks are pre-programmed and great importance is placed on flexibility and short response times. This explains, for example, why there is a panel processing system complete with interim storage upstream of the production line. From here, planking material can be delivered to the work tables preassembled to ease heavier workloads at this station. Actual element production at Blumer-Lehmann begins by inserting and nailing the timber frame on table 1. Planking is applied on table 2, where the panels are also cut to size by the WEINMANN multifunction bridge and the required openings are created. Dividing these process steps over two tables shortens the system cycle time: the next timber frame can be inserted on table 1 while the previous element is being processed on table 2. This avoids bottlenecks in the time-consuming process of timber frame construction. Beams for ceiling and roof elements are inserted on table 2, which is equipped with the appropriate fixing devices. After planking, the frames are turned between table 2 and table 3. On table 3, the insulation and installation materials are inserted - these are also time-consuming process steps, which is why the system is designed so that they can also be performed simultaneously on table 4. Transported across to table 5, the element is then planked and processed by the multifunction bridge once more. From table 5, the timber frame elements produced are placed on a distribution trolley via a vertical wall track. From there, they are transferred onto an overhead crane, which then loads them onto pallets. Elements to be further processed for modular buildings are passed on to a further wall track, which ends in the module production area. There, the elements are removed at ten module assembly points, where they are put together as modules and removed from the line as a finished product. Only the uppermost layer of the flooring is applied at the construction site later on. The finished modules, which are up to 12.00 m in length, are stored in special storage locations on the company premises, from which they are transported to the construction site when construction begins.
Conclusion
Looking back, thanks to its investment in the new production system, Blumer-Lehmann AG has achieved its primary objectives - a clearly structured production process and a consistently high level of quality. Combined with the accompanying peripheral measures, the company has also been able to reduce its production times significantly and lower production costs, despite the increased costs at the work preparation stage. This new technology also offers some small advantages when it comes to marketing. According to Richard Jussel, "Having a production hall that is clearly structured and efficiently arranged fits our image well. The system and its precise, easy-to-follow production steps impress both architects and private customers. Ultimately, it assures them that we supply a high level of quality with minimized risks. However, it's not enough just to buy such a system; you have to talk about it as well."
Source images: Blumer-Lehmann AG
An article from the magazine BAUEN MIT HOLZ, 11/ 2017. Here you can read the article.
“Having a production hall that is clearly structured and efficiently arranged fits our image well. The system and its precise, easy-to-follow production steps impress both architects and private customers. Ultimately, it assures them that we supply a high level of quality with minimized risks.”General Manager Richard Jussel, Blumer-Lehmann AG
Blumer-Lehmann AG
Blumer-Lehmann AG designs and builds individual buildings using timber - from housing and commercial, industrial and agricultural structures to public buildings and free forms. The team of Blumer-Lehmann not only creates new builds, but also converts and renovates existing structures.
Find out more here!