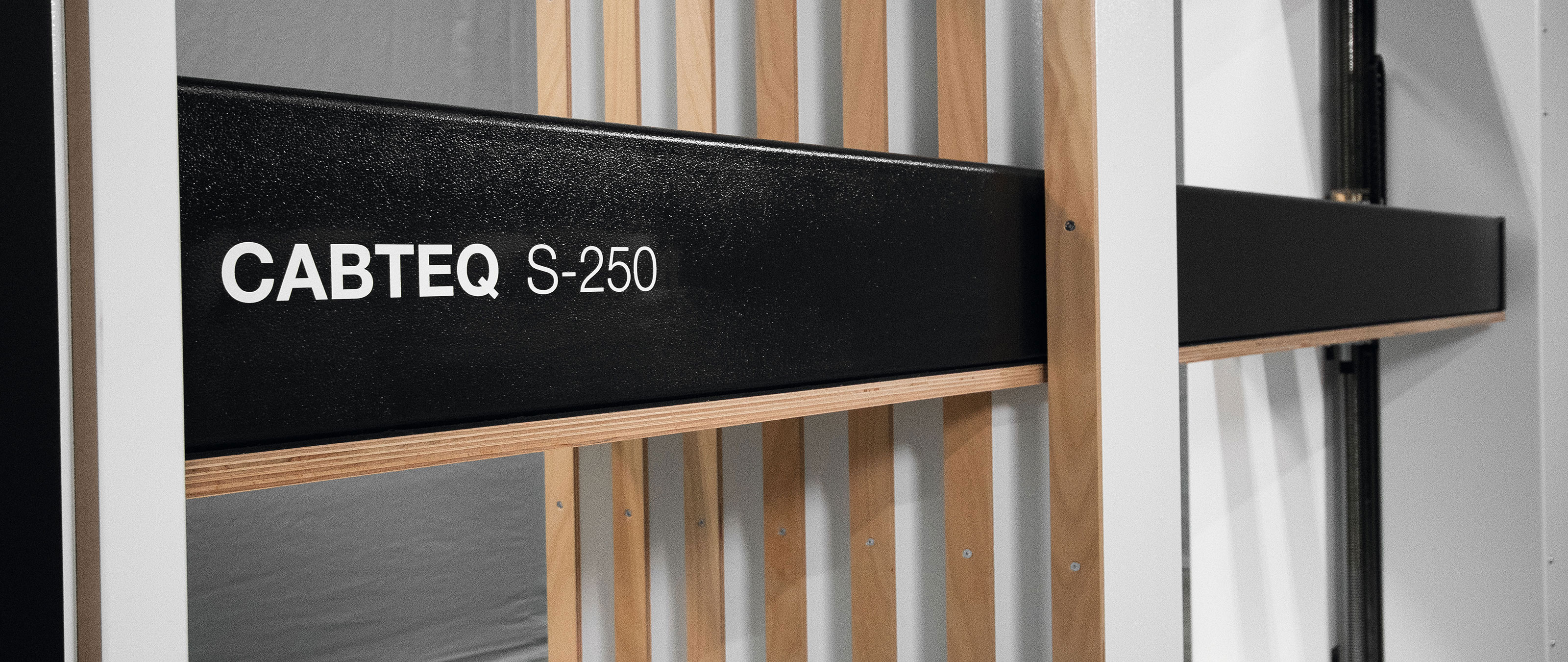
Specialist kitchen furniture manufacturer, Kent Home Improvements, was set up in 1970s. With a turnover of around £2½ million, the company has built a reputation for designing and producing high quality furniture components for the independent kitchen trade.
“Although the company is over 50 years old, it is only in the last six years that the business has grown exponentially,” enthuses Dan Endicott, general manager at Kent Home Improvements. He continues, “The expansion is down to the investment the new owners (who bought the business in 2017) have made in machinery and staff.
“The latest investment was for a HOMAG CABTEQ S-250 press. The company has been buying HOMAG machinery for over 40 years and has always found its equipment and software to be superb. We believe it is the best in the market and offers outstanding value for money.
“Our old carcass press was dying and we no longer needed such a big press. We wanted a robust, efficient and simple to operate carcass press to replace it and so we turned to HOMAG.”
A visit to the HOMAG Showroom
“To ensure we invested in the right model, we attended one of HOMAG’s Open House days at its Castle Donington showroom. Seeing how easy to operate the CABTEQ presses are, and the perfectly square units they produce, gave us the confidence to place an order for the CABTEQ S-250 model.
“As the last step in production before packaging and delivery, the assembly quality has a significant impact on the end customer‘s satisfaction with the product. So for us, when it comes to building kitchens, cleanly pressed cabinets are a key sign of quality in pre-assembled furniture.
“The HOMAG CABTEQ S-250 delivers on every front. It’s a reliable, high performance press that ensures all our cabinets are accurately and squarely aligned. Another bonus is you need no prior knowledge to operate the press; it’s simply a question of placing the cabinet in the press and pushing the start button.
“The plates move from their starting position to the pressing position at rapid speed. Then, just prior to connecting with the cabinet, the speed switches automatically to the slower pressing speed. This system minimises the time needed for the pressing process.”
Versatile, powerful and reliable
The CABTEQ S-250 model can handle a diverse range of product sizes – from cabinets (l) 150 x (w) 250 x (h) 150 mm up to (l) 3000 x (w) 900 x (h)1400 mm. With a pressing pressure range from 12 – 18 kN in both vertical and horizontal planes, the pressing force can be adjusted as required. This is simple to do on the control panel and ensures the pressure is distributed completely evenly on all sides of the cabinet.
Dan Endicott again, “Our new press from HOMAG has speeded up our production process as we no longer have to do any manual clamping. More importantly, perhaps, it has improved the quality of every finished product we manufacture – we can now be certain each cabinet will be perfectly square.
“Our long-standing relationship with HOMAG is based on trust and service. All the HOMAG people are friendly, professional and extremely knowledgeable; they are always there on the end of a phone if we need anything, and its machinery is reliable and delivers lifetime value for money,” concludes Endicott.
If you would like more information or a demonstration of any of the HOMAG machinery and software, please contact HOMAG UK on 01332 856500.
“Our long-standing relationship with HOMAG is based on trust and service. All the HOMAG people are friendly, professional and extremely knowledgeable; they are always there on the end of a phone if we need anything, and it's machinery is reliable and delivers lifetime value for money.”Dan Endicott, General Manager