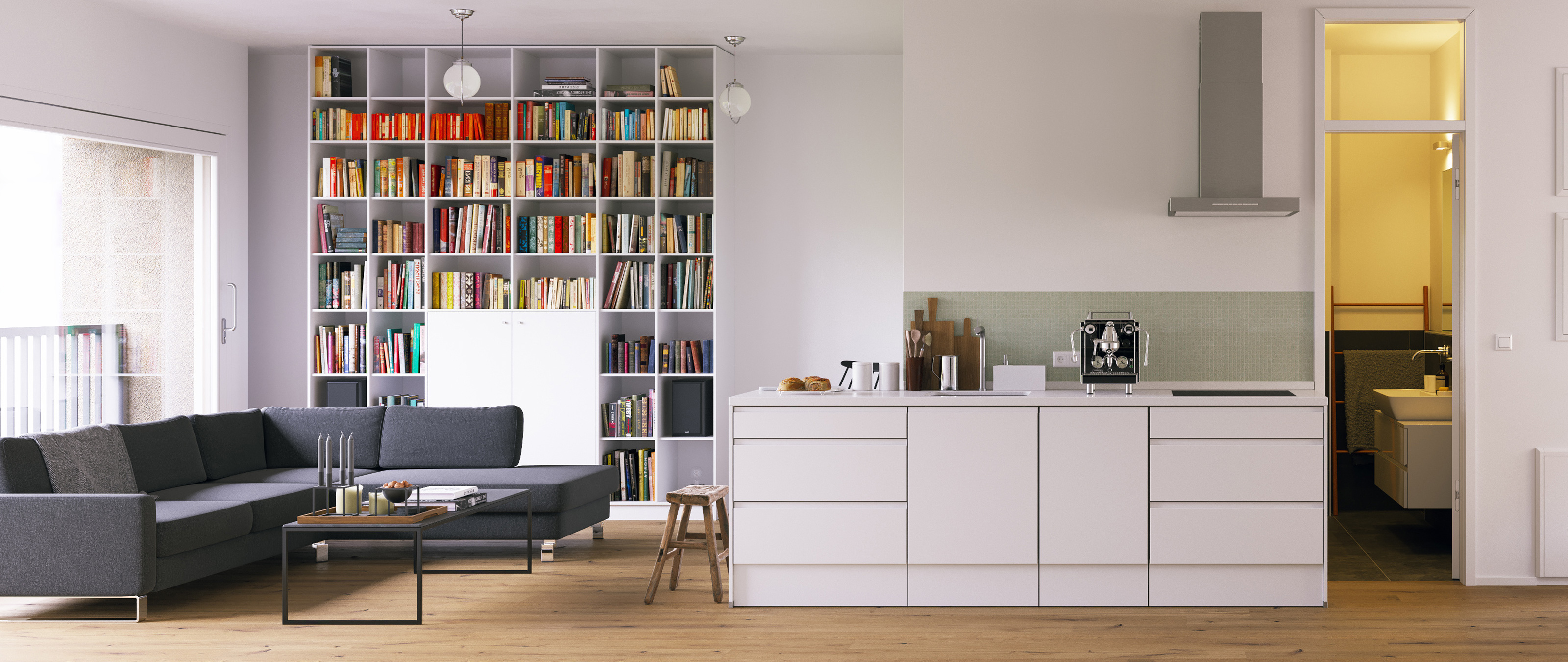
ECF Ltd has a turnover in excess of £21 million and growing...
“Our original factory (known as Plant 1) was running at full capacity,” explains Craig Cooper, production and development manager at ECF Ltd. He continues, “the huge success of our in-house manufactured products such as the Gaddesby Kitchens, Volante Bedrooms and Greyhouse Bathrooms meant we had to add capacity to the manufacturing facility.
“With the faster than expected growth rate of our kitchen, bedroom and bathroom ranges, we took the decision to invest in another state-of-the-art manufacturing plant (Plant 2). This new facility was to be dedicated to the manufacture of our assembled furniture ranges. It had to be as flexible as possible to enable us to carry more stock decors and to broaden our Gaddesby Kitchens offer.
“I had a good understanding of the production line that would be required and, after various meetings with Simon Brooks and personnel from HOMAG Germany, we finalised the machinery specification list. The heart of the production cell is an automated storage and retrieval system coupled with two CNC nesting machines, complete with automatic labelling.
“This equipment performs the tasks of board storage, panel sizing, part labelling, routing and vertical drilling. All the horizontal drilling, gluing and dowel insertion is handled by an ABD 260 drilling and dowelling machine. For the edge banding we specified two HOMAG 2492 machines, both equipped with a PUR gluing facility and one which has airTec for invisible joints. Completing the new equipment in the cell is the MDE 120 carcass press with cabinet erector and rotation table for the cabinet assembly.
“We also relocated an existing HOMAG BHX 055 vertical CNC from Plant 1 to Plant 2 to process one-off panel boring and special door/drawer drilling.”
Making the right choice
“Naturally, for an investment of this size we talked to a number of other suppliers, but at the end of the day we felt comfortable with the relationship we have built up with HOMAG over the last 12 years or so. Most of our machinery in Plant 1 comes from HOMAG so we have considerable knowledge and understanding of the equipment and software.
“To change to another machine supplier would have added unnecessary risk to our investment in terms of machine reliability, sales support and service. With HOMAG, on the other hand, we know exactly what we are going to get. Our working relationship with HOMAG’s sales and marketing director, Simon Brooks, is excellent; it is so important to have complete trust both in the hardware and the company you are buying from when investing large sums of money into a project such as this.
“It wasn’t, however, a done deal. It was imperative for me to see all the equipment in action either in real world factories or trade shows. I would never buy machines of this type ‘off plan’. I need to see them working, I need to interact with them and ask questions in order to fully understand their benefits - as well as their limitations. Then, and only then, can I be confident in asking for the funding from our board of Directors.”
Flexibility with automation
“There were a number of key benefits the new production cell had to deliver, two of the most important of which were flexibility and a more automated approach to our just-in-time manufacturing ethos. The TLF 211 storage and retrieval system is fundamental to delivering these goals.
“Manual materials handling has been reduced considerably. Our daily delivery of MFC is forked straight into the loading area of the TLF 211. The board is automatically stored and then, as required, it is retrieved, pre-sorted, labelled, cut and drilled before anyone even touches it.
“Not only that, but all of the pre-sorting can be carried out during the evening with lights-out operation, ready for the next day’s production run. The front end processes of sorting, loading, labelling, sizing, drilling and routing are all completed with just the one operator on the outfeed of the two CNCs. With less sophisticated machinery, you would need at least three operators to carry out those processes in the volumes we require.”
Reliable, fast production with premium quality
“This manufacturing cell has enabled us to increase capacity with improved product quality. What’s more it is reliable. The ABD 260 is a case in point. It’s a quick, no-nonsense machine which does its job efficiently and accurately. All three processes of horizontal drilling, glue injection and dowel insertion are carried out in one pass – and its CNC control suits our batch-size-one manufacturing technique perfectly.
“We have always been fans of PUR glue because of its excellent water resistant nature and the cleaner glue line you get with PUR. Old fashioned EVA glue just isn’t good enough for our products which is why we specified both edge banders to come with a PUR gluing system.
“It was also important we had a ‘zero-joint’ capability for those highly visible parts which is why we specified airTec on one of the edge banders. The airTec is only used for the cabinet fascias and will be used for future products which require a seamless transition from panel to edge.
“Overall, the cell has delivered huge time savings and increased efficiencies whilst giving us far more flexibility. It has allowed us to better service the builder and developer market as well as our highly valued existing customers. The small accuracy tolerance of the HOMAG CNCs enables us to create superb quality cabinets – worthy of our Gaddesby, Greyhouse and Volante brands.
“The cell’s performance has been amazing. We planned for a three year return on investment, but with things going the way they are, it looks like being as quick as two years. With a complex set up like this, teething problems are almost inevitable and so these are always factored into the first six months of production planning. We are, however, ready to ramp-up to full production after just three months,” concludes a delighted Craig Cooper.
If you would like more information or a demonstration of any HOMAG machinery or software please contact HOMAG UK on 01332 856424.
“Overall, the cell has delivered huge time savings and increased efficiencies whilst giving us far more flexibility. It has allowed us to better service the builder and developer market as well as our highly valued existing customers. The small accuracy tolerance of the HOMAG CNCs enables us to create superb quality cabinets”Craig Cooper, production and development manager at ECF Ltd