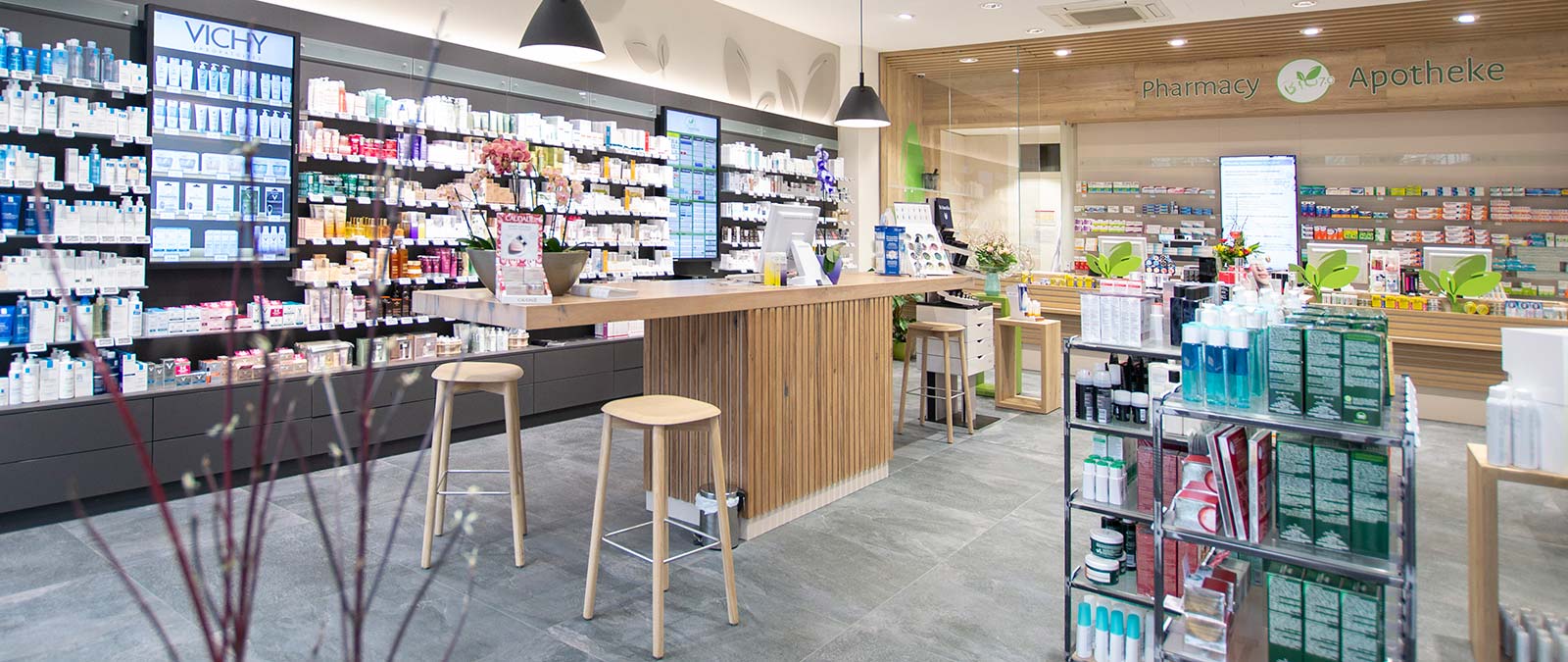
Saw-storage combinations offer users a number of benefits: throughput, quality, ergonomics, transparency and the ability to display the utilization factor of materials to name just a few. For Rolf Rissel Objekteinrichtungen GmbH in Berlin, one aspect in particular has stood out since the commissioning of its new HOMAG system: the new pace of production.
The drugstore landscape is changing and has been for many years. In 2010, there were more than 21,000 drugstores in Germany; today, however, there are just 18,000. Experts expect that this figure will decrease further to 15,000 in the coming years. There are several reasons for this. One reason is the introduction of electronic prescriptions and online retailing. Regardless of the reasons, the operators of physical drugstores are having to look closely at their business models — not the basic principle, but rather any features that could make the difference to the business.
Focus on emotions
The Berlin-based company Rolf Rissel is not just accompanying drugstores on this journey; the furnisher is also helping them to design and shape their futures. The business, which operates from Spandau in Berlin, designs complete concepts that it then implements in their entirety. A series of interior architects, designers, wood engineers and master carpenters are responsible for ensuring that every single customer requirement is met, even those for logo development or external advertising. The company offers a comprehensive service while also meeting individual customer requirements, providing both the ideas and the implementation of these ideas. "Transforming emotions into custom wood, glass and metal structures is at the heart of what we do," stresses Managing Director and proprietor Karl Löffl.
Rolf Rissel Objekteinrichtungen was founded in 2003 from a predecessor company. In 2007, the company moved from the outskirts of Berlin to Spandau. This was a significant step for the furnisher, as the location's excellent access to the freeway, intercity express rail line, buses, subways and regional trains meant the company was now very well connected. Since then, it has been much easier for customers from Hamburg, Frankfurt and Munich to visit the company. "Berlin is also very attractive," says Löffl. "But above all, we can now demonstrate our production process and products to customers and allow them to touch them too."
Doing it well
Rissel's main focus is the healthcare sector. The company's predecessor also specialized in drugstores, although it kept the sales structures very small for capacity reasons. "We have changed that and strengthened sales." The company is now reaping the benefits: In the past, in addition to the drugstores, the company fitted out one to two medical practices per year; now, it's ten to twelve per year. "We're also gaining an increasing foothold in the area of clinics and are now fitting out patient rooms and laboratories. We have even worked for the Charité university hospital." The private sector is also becoming increasingly important to the company, meaning that Rissel now has four main areas of business: drugstores, medical practices, clinics and private customers. "And everything that is a special requirement, where the furniture is not available off the shelf," Löffl adds, is number five. Previously, the company's services were only available in the north of Germany. Now, however, the company is able to cover the entire country. The proprietor is already looking to tomorrow: "If we do it well, then we will be well-equipped for the future."
Improving performance
Rissel recently took a significant step in improving the beginning of its production chain: Installing a saw-storage combination from HOMAG. This was preceded by a visit to the Holz-Handwerk trade fair in Nuremberg in 2018, where the company was given in-depth information about the system. "The advice back then was perfect, it couldn't have been better," remembers Löffl. "Of course, we spoke to other providers and got other quotes as well. We weren't looking for the cheapest price, we were looking for performance and trust. Once we had visited a company that was already using this system, it was clear: We had to work together with HOMAG to achieve the same thing." The organization already had a history of working with HOMAG: Since 2016, the Spandau-based company has been working with an edge banding machine and part return from Schopfloch.
And now it was time for the new saw-storage combination. "We had a horizontal saw before," remembers Löffl. "But over the years, it had become very imprecise. And the storage technology no longer met modern standards either. On some days, we had to spend more time moving panels with a forklift truck than we could on cutting. So we were keen to improve performance in storage and sawing." In this case, improving performance meant installing automatic panel storage for stacking 600 to 1000 panels, improving access for truck deliveries, automatic return to storage from a specific panel size, "and, very importantly for us, offcuts storage with a management system and strict organization."
For individual production and small series
Rissel improved performance in panel cutting by installing their own SAWTEQ B-300. "As the basic model for series 3, the pressure beam saw is designed for batch size 1 production and the production of smaller series. At the same time, it is designed to cut single panels and panel stacks made from all standard materials, for which it uses an 80 mm saw blade projection," reports Thomas Nesemeier, Sales Manager North at the HOMAG Group. Speeds of 130 m/min on the saw carriage and 90 m/min on the program fence enable a high level of productivity in division processes. The basis is a main saw motor that provides a power of 11 kW. At Rissel, the SAWTEQ B-300 allows lengths of up to 3200 mm to be cut.
"The panel saw is fed by a STORETEQ S-200 storage system," adds Nesemeier. "Here, the ST 61 suction cross rail handles coated panels from a thickness of 8 mm as well as unprocessed panels from 12 mm. With a bridge speed of 60 m/min, a carriage speed of 80 m/min and a lift drive speed of 30 m/min, the storage system is designed for workpiece lengths of 2000 to 4200 mm and workpiece widths of 800 to 2200 mm and can therefore be adapted to suit an extremely wide range of materials and space requirements." The cross rail can be used to transport panels weighing up to a maximum of 250 kg. Automatic adjustment dependent on the size of the panels as well as an automatic separating device ensure safe handling.
Work preparation redefined
Commissioning of the system and training on the use of the CADmatic 5 operating software, the Cut Rite cutting optimization software and the woodStore storage software took place around three months ago. A little later, iX from imos was also introduced with help from an external advisor. Since then, two employees have been assigned primary responsibility for the CAD/CAM system, and further employees will be trained in the coming months. As part of this process, HOMAG has configured the necessary interfaces and organized the data transfer. The specifications from imos can now be used for cutting and labeling. The usual information accompanies the parts: customer, order, part designation, material and dimensions, edging. HOMAG has also implemented barcode recognition on a downstream processing center. This allows components to be scanned here. It is also possible to process any programs that have been called up.
Orderly and transparent
Looking at the effects of the panel storage, Löffl is keen to highlight one aspect in particular: "Order, order and more order." Almost 1000 panels have been placed in storage without any damage occurring. The panels are stored and managed in mixed stacks; the storage system presorts the panels during free time. "Previously, we needed to have one employee presorting panels using a forklift truck at all times. This meant that we could only cut a few panels in each shift and for the remaining time the machine was idle," reports Löffl. "Now, the employees know what they want to cut in the afternoon and they enter the corresponding patterns. The storage system then starts restacking. When the employee arrives at the machine, work starts immediately."
Logistics has also been restructured as storage racks have been freed up and areas up to 20 m long are now available across three tiers. Nowadays, the panel stacks are simply placed in the return to storage area of the storage system and the system then places them in storage automatically. The management of the panel offcuts is now also transparent: "We have a large offcuts storage that is orderly and clear and even has an integrated escape route. We don't need to waste time searching anymore."
Breaking out of old habits
When it comes to cutting, the SAWTEQ B-300 has almost doubled throughput. "The question was, how do we pass that on to production?" By reorganizing the work, the proprietor emphasizes. The designers previously had to write out parts lists by hand; now they can send the lists directly to the machine, meaning that the manager of the workshop now has time to coordinate production, for quality control or to solve any problems that arise. "The most important part, however, is that the entirety of the work preparation now comes from iX and the storage system controls the jobs. The storage system now sets the pace," emphasizes Löffl. "Previously, these paces were irregular. Now, the rate is predefined." To allow this rate to be transferred to the downstream production without any issues, Rissel has also sought to improve performance in the processing centers. At the beginning of October, the furnisher replaced an older processing center and now two equally powerful machines keep up the pace of production as it moves toward the assembly area. Löffl is certain that "due to the pace of the saw-storage combination and the new production throughfeed, we can no longer work to old patterns." This new pace is perfect for the healthcare sector.
„Now, the employees know what they want to cut in the afternoon and they enter the corresponding patterns. The storage system then starts restacking. When the employee arrives at the machine, work starts immediately.“Karl Löffl, Managing director and owner of Rolf Rissel Objekteinrichtungen GmbH