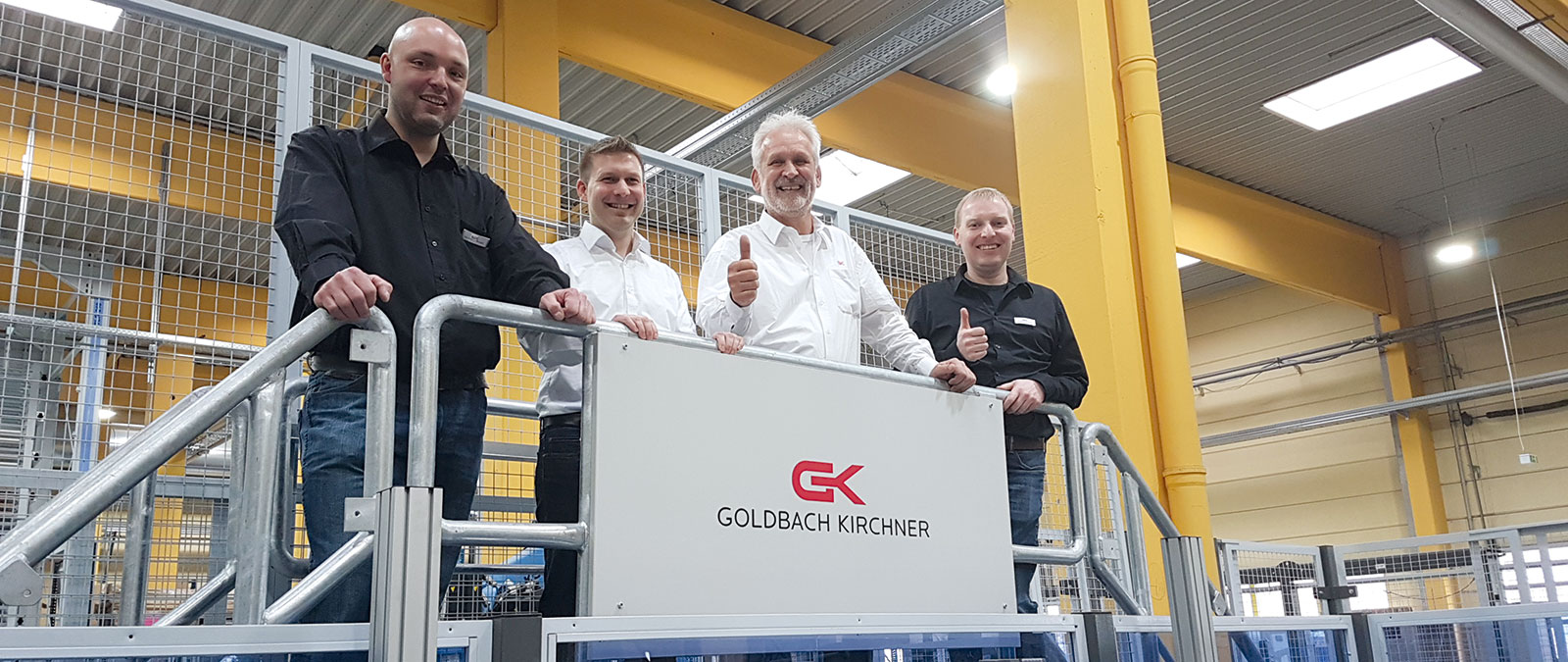
Lo specialista di interni Goldbach Kirchner Raumconcepte di Geiselbach ha aumentato la sua capacità produttiva in modo radicale: su un ex sito per la produzione di mobili a Dessau è nato, in collaborazione con HOMAG Group, un impianto produttivo altamente automatizzato per mobili e componenti rettangolari secondo i principi dell'Industria 4.0.
Goldbach Kirchner Raumconcepte GmbH è un'azienda innovativa a conduzione familiare di terza generazione. La Bassa Franconia è sinonimo di sistemi di pareti divisorie e pareti attrezzate di elevata qualità, produzione in serie e finiture interne di alto livello, attribuisce molto valore a uno sviluppo proprio e sostenibile oltre a una produzione "Made in Germany".
Pur mantenendo la sua solidità, la storia dell'azienda è sempre stata caratterizzata da audaci decisioni imprenditoriali: tutto è cominciato dal fondatore, Jakob Kirchner, che con la domanda di brevetto della "scala retrattile" e la propria produzione a Geiselbach ha dato il via nel 1922 a una storia di successo.
L'attuale amministratore, Bernd Kirchner, non è da meno. Ha ampliato gradualmente l'azienda in una grande falegnameria e nel 2004 ha fatto un passo importante: rilevare la Goldbach Raumconcepte GmbH di Goldbach presso Aschaffenburg. In precedenza l'azienda si era concentrata per decenni sulla produzione di sistemi di pareti attrezzate e di pareti divisorie oltre a mobili per ufficio. Nello stesso anno Kirchner trasferì lo Sviluppo e la Produzione dei prodotti Goldbach a Geiselbach.
La cooperazione tra la Kirchner Schreinerei Innenausbau GmbH e la Goldbach Raumconcepte GmbH ha portato molto presto a sinergie in innumerevoli settori aziendali. Nel 2006 è avvenuta la fusione finale: dalle due aziende è nata l'odierna Goldbach Kirchner Raumconcepte GmbH con sede a Geiselbach che si occupa dello sviluppo e della produzione di sistemi di pareti attrezzate e divisorie di alta qualità nonché di finiture interne con oggetti ricercati.
Da quel momento in poi c'erano tutti i segni di crescita per il potente interior designer. E ciò è stato evidente nel 2015 in un'altra fase strategicamente significativa: Bernd Kirchner ha rilevato un'area produttiva a Dessau non lontano dalla storica e rinomata Bauhaus.
"Durante una sciata, un conoscente ha fatto riferimento al fatto che l'azienda lì residente avesse presentato istanza di fallimento e l'intera area sarebbe stata messa in vendita. Ai tempi della DDR esisteva un mobilificio e anche in seguito si era trattato il legno. Finora l'idea di base era di usare le strutture esistenti, non il contrario. Alla fine mi decisi e andai a fare una visita, tuttavia era chiaro che non sarebbe stato semplice produrre lì. Da una parte a causa dello stato dell'edificio, dall'altra per il flusso del materiale poco efficiente su lunghissimi trasportatori a rulli e un parco macchine decisamente obsoleto", afferma l'uomo d'affari.
Tuttavia, Kirchner ha visto del potenziale nei beni immobili esistenti. "A Geiselbach non abbiamo più alcuna possibilità di ampliamento, ma nella nostra situazione di mercato potremmo sicuramente crescere aumentando i volumi produttivi. Così è venuta l'idea di una produzione fortemente collegata in rete a Dessau".
Il responsabile di produzione Sebastian Schmidt aggiunge: "La visione era ed è quella di inviare a Dessau, dopo la progettazione dei prodotti a Geiselbach, solo i set di dati per mobili e componenti rettangolari. E poi basta premere un pulsante e la produzione avviene li in modo altamente automatizzata con un impiego minimo di personale ".
Una volta che fu chiaro che uno dei nuovi capannoni nella Sassonia-Anhalt, utilizzato fino a poco tempo prima come magazzino, soddisfaceva le condizioni necessarie, Kirchner si è deciso ad acquistarlo. Già poco dopo l'acquisizione dell'area, compresi i beni immobili, nell'aprile del 2015, solo un mese dopo la LIGNA sono iniziati i primi progetti per la nuova linea di produzione.
"Potendo progettare da zero sul tavolo da disegno, abbiamo potuto realizzare un impianto di produzione orientato al futuro. E con il quale siamo assolutamente all'altezza di soddisfare gli ordini individuali dei nostri clienti. Grazie alla produzione a Dessau riusciamo ad essere assolutamente convincenti sia nella produzione in serie sia nella produzione lotto 1, realizzando, quindi, il nostro desiderio di essere un produttore veramente innovativo", prosegue Kirchner.
In definitiva, questo grande progetto è stato implementato insieme a HOMAG Group. "La collaborazione tra Goldbach Kirchner e HOMAG prosegue già dagli anni '80. La prima macchina era stata all'epoca una sezionatrice HOLZMA. Naturalmente, per l'impianto a Dessau abbiamo preso in considerazione anche altri produttori, ma alla fine ci ha convinti, ancora una volta, l'efficienza di HOMAG grazie a un concetto di impianto altamente innovativo che soddisfaceva tutti i nostri requisiti in termini di macchine e software", riassume Schmidt.
La lavorazione dei materiali impiegati – pannelli truciolari, MDF, listellari, pannelli leggeri e pannelli rivestiti in melammina con e senza pellicola protettiva nonché un formato di pannelli grezzi massimo di 3320 x 2100 mm – inizia con un magazzino orizzontale STORETEQ S-500 (TLF 411) lungo circa 50 metri e largo 10 metri. Prevede 40 posizioni magazzino per il formato 2800 x 2100 mm e otto posizioni per il formato 4100 x 2100 mm. La capacità massima nel magazzino orizzontale nel caso di materiali spessi 19 millimetri è di circa 5040 pannelli.
Collegata al magazzino, anche se non nell'intera linea, è presente una sezionatrice di pannelli SAWTEQ B-300 (HPP 300) con etichettatura sul dispositivo di pressione. All'occorrenza può essere usata per tagli individuali.
Tuttavia, il flusso di materiale reale trascura questa sezionatrice, perché il portale del magazzino gestisce l'ingresso di una sezionatrice SAWTEQ B-320 (HPS 320) tramite robot. Qui il taglio dei pannelli grezzi viene eseguito in base ai dati dei pezzi, il robot assume l'intera gestione, compreso il trasferimento dopo la lavorazione (etichettatura compresa). Questa parte di impianto crea fino a 1500 pezzi a turno a seconda dello schema di taglio.
Alla SAWTEQ B-320 (HPS 320) segue un magazzino intermedio polmone SORTEQ H-600 (TPL 220) con 20 piani e un immagazzinamento a due corsie. Al tempo stesso esiste la possibilità di espellere prima del magazzino intermedio i pezzi piccoli di dimensioni inferiori a 240 x 140 x 10 mm poiché non possono essere lavorati nelle successive aree macchina. La stessa procedura viene utilizzata per i pezzi residui o per i pezzi già finiti, ad esempio gli schienali.
"Per noi è molto importante poter escludere in caso di emergenza determinate aree macchina e avere accesso a più posizioni. Nel caso normale i pezzi attraversano la linea dal pannello grezzo al pezzo finito, bordatura e foratura comprese. Ma in caso di guasto a una macchina, la nostra speciale progettazione del ciclo di lavorazione impedisce che l'intera linea rimanga ferma. A seconda del carico e della pressione può essere "di vitale importanza". Per sicurezza, in fase di progettazione dell'impianto abbiamo già previsto gli "scenari peggiori", tra cui, ad esempio, una caduta di tensione", spiega il dirigente responsabile dello stabilimento di Dessau Christian Stoll.
Alla posizione di magazzino intermedio segue una bordatrice EDGETEQ S-800 (KFR 610) con ritorno pezzi LOOPTEQ C-500 (TFU 820), per bordare i pezzi, all'occorrenza, su uno o più lati. A scelta si utilizza colla PU oppure la bordatura mediante laser. Vengono utilizzati bordi in ABS, PP e melammina, per la lavorazione della scanalatura la macchina è stata dotata di due gruppi di tipo SF 62.
Successivamente si passa a un trasporto pezzi su due livelli con pulizia automatica dei due lati del pannello. Anche questa parte di impianto funziona da piccolo polmone. Da lì si arriva in un magazzino di smistamento SORTEQ R-200 (TLB 320). Con un immagazzinamento a doppia profondità, questo impianto contiene circa 1500 componenti e serve a smistare i pezzi già bordati. Per tutto ciò che non richiede ulteriori lavorazioni, al magazzino segue l'accatastamento diretto RKR 180 mediante robot. Allo stesso modo, in questo punto si possono caricare i pezzi che richiedono forature speciali.
In fase di accatastamento il robot forma automaticamente le posizioni in base ai recordi di dati individuali e ruota, inoltre, i pezzi per l'impianto di foratura. La foratrice in continuo DRILLTEQ L-500 (ABH 100) rappresenta la parte finale dell'impianto altamente automatizzato. Qui avviene la lavorazione su tutti i sei lati in modalità continua senza contorni di disturbo nonché l’inserimento spine in direzione X. Inoltre viene effettuata una misurazione al 100% e vi è un magazzino intermedio per pezzi finiti per 30 componenti.
Alla base di tutto vi è il sistema superiore di produzione HOMAG ControllerMES. Esso genera i dati per le rispettive parti dell'impianto in modo tale che la lavorazione possa avvenire a lotto 1. Nel caso della Goldbach Kirchner, le informazioni sul pezzo provengono dal software Kuhnle e CAD+T – ControllerMES rielabora questi dati poi per la produzione.
Ad esempio, se in fase di progettazione a Geiselbach viene stabilito che, per motivi estetici, il bordo deve essere applicato solo trasversalmente invece che longitudinalmente, il sistema ne terrà ovviamente conto e tutto l'impianto farà in modo che il pezzo entri correttamente.
A seconda dei dati forniti dal ControllerMES, la sezionatrice realizza i rispettivi schemi di taglio in modo autonomo, proprio come l'impianto di foratura richiama il programma CNC necessario per il relativo componente. Inoltre è anche possibile in qualunque momento la produzione di pezzi veloci. Anche in presenza di errori dovuti ai controlli di qualità automatici, ControllerMES reagisce: il sistema blocca seduta stante tutta la commessa.
L'inizio della produzione corrisponde a quattro giorni prima della data di consegna concordata di un mobile, per questo motivo, i pezzi necessari e i pezzi possibili vengono ottimizzati dal punto di vista degli scarti. Il magazzino funziona quasi continuamente. La precedenza di alcuni pannelli risulta dalle priorità precedentemente stabilite, di cui tiene conto il ControllerMES in fase di controllo del magazzino. Quindi la sera si preseleziona automaticamente l'avvio della produzione per il giorno successivo. Gli ordini al magazzino ottimizzati passano ogni due ore dalle operazioni preliminari di produzione a Geiselbach a Dessau.
Se per un ordine sono necessari pezzi di forma libera, la produzione avviene a Geiselbach. Lo stesso vale per i mobili complessi la cui produzione avverrebbe con scarsa efficienza nel nuovo impianto. "Abbiamo una movimentazione costante all'interno dell'azienda, a seconda dell'ordine decidiamo dove riunire i pezzi di un ordine. Ciò può avvenire anche direttamente in cantiere", prosegue Schmidt.
Oltre a HOMAG, l'unico altro produttore coinvolto nella costruzione del nuovo stabilimento di produzione era la Scheuch Ligno, esperta nel campo dell'aspirazione: per la produzione di mobili è stato fornito un impianto "Sepas-Plus" con una potenza di aspirazione di 80000 metri cubi all'ora, un'"unità Eta-max" con ventilatori ad alto rendimento con un'efficienza pari all'85% nonché un filtro di impulso Scheuch-Ligno con deposito trucioli integrato. Il trasportatore pneumatico dal filtro di impulso al silo per trucioli centrale supera un percorso di circa 85 metri, la portata è di 2800 chilogrammi all'ora. Il funzionamento a intervalli garantisce un particolare risparmio energetico.
Il nuovo impianto di produzione HOMAG è stato messo in funzione nel mese di giugno 2017 e ha raggiunto il pieno regime a ottobre 2017. La portata media era di 600 - 800 componenti a turno.
Per cui oggi ci si adopera per limare ancora la massima efficienza: "Se l'impianto funziona a pieno regime, c'è bisogno ancora di un nuovo dipendente, al momento ne sono presenti tre in loco. E ci sono ancora molte idee. Stiamo pensando di utilizzare una soluzione che sfrutti la tecnologia RFID al posto del codice a barre. E prima o poi vorremmo avere sofisticati sistemi di telecamera in loco per monitorare l'impianto e semplificare la manutenzione all'interno dell'azienda. Una cosa è chiara: questo impianto rappresenta lo stato dell'arte e in questa forma altamente automatizzata, probabilmente uno dei più moderni al mondo. In linea di principio, l'incarnazione dell'idea alla base di Industria 4.0. Questo è il motivo per cui desideriamo entrare in contatto con altri fornitori. Finora solo un produttore di materiali legnosi fornisce i pannelli già muniti di codice a barre che può essere letto dal nostro impianto", spiega Schmidt.
E abbiamo anche progetti per il sito: "Dietro lo stabilimento di produzione attualmente in uso, c'è ancora molto prato verde. C'è spazio sufficiente per spostare, ad esempio, l'Amministrazione in un nuovo edificio ed eventualmente allestire un moderno showroom", dice Kirchner.
Videos
Ti preghiamo di confermare che quando utilizzi YouTube, dati come il tuo indirizzo IP, l'identificatore del browser e simili potrebbero essere trasmessi a Google.
» Tutela della privacy
Video: Uno degli impianti Industria 4.0 più moderno nel settore dei mobili presso Goldbach Kirchner.